Bio-Hazards & Pathogens Spread Rife in the Agricultural Industry
Industrial-scale farming enterprises are facing a problem – the spread of pathogen-infested manure onto farmland. Intensification of pig, poultry and dairy farming and manure transportation mean that there has been an increase in cross-infection. Manure needs to be handled properly at point of origin to ensure pathogen-spread risks are minimised.
Manure and animal by-products are high risk depositories for pathogens and harmful viruses. The food industry has rightly implemented strict regulations to reduce transmission risks and encourage safe utilisation of manure. Stronga’s bio-secure steam pasteurisation technologies allow manure to be reliably cleaned of harmful bacteria so it can be applied to soil for its wonderful enriching qualities.
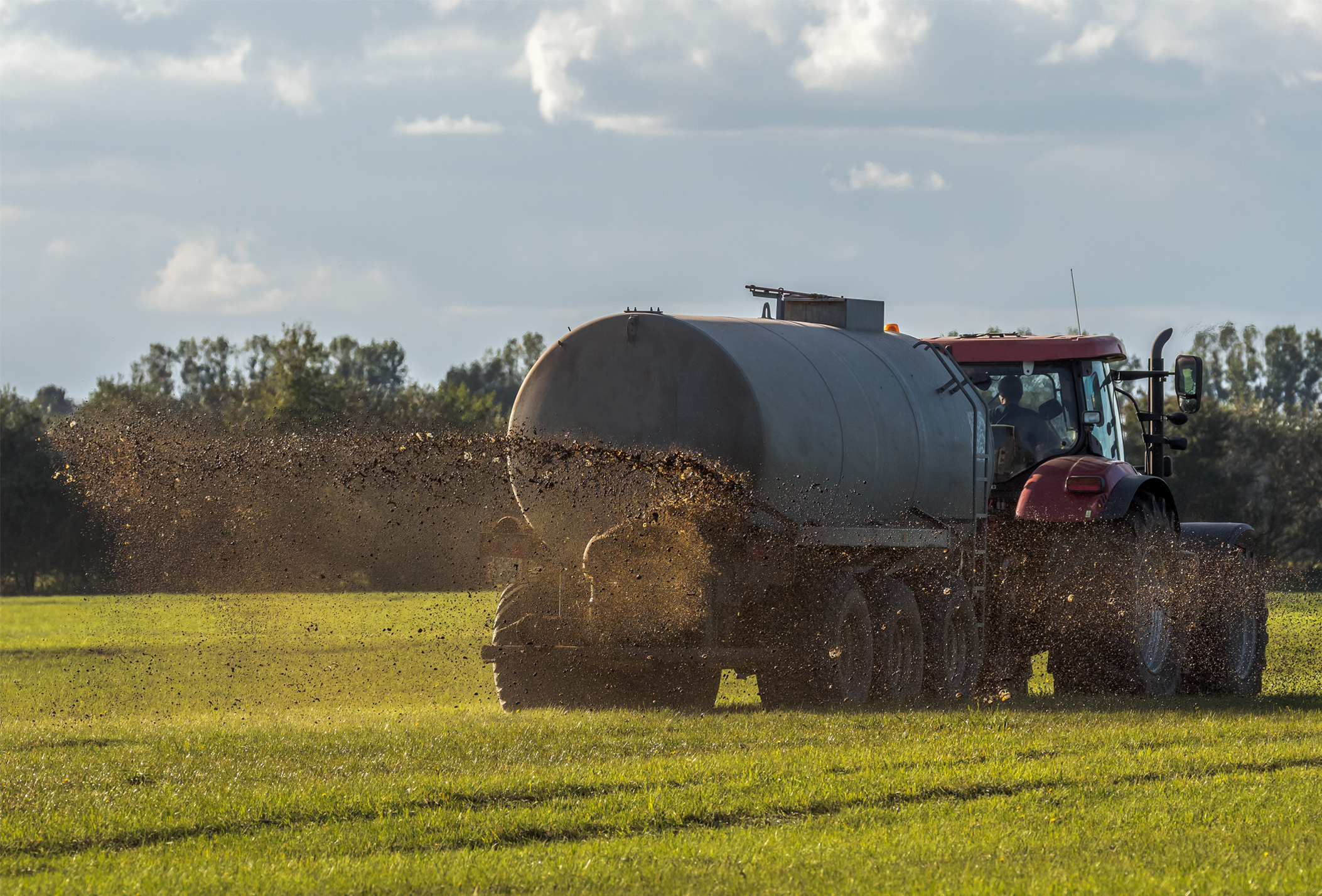
The high risks associated with pathogen spread via manures, especially within the vegetable sector and food chain, mean that pasteurisation and sterilisation strategies must be adopted to dramatically reduce risks of zoonotic disease; including, Salmonella, E-coli and Listeria etc. These diseases are illustrated in the chart below which shows the total concentration of bacteria, phage and the most abundant ARGs in manure.
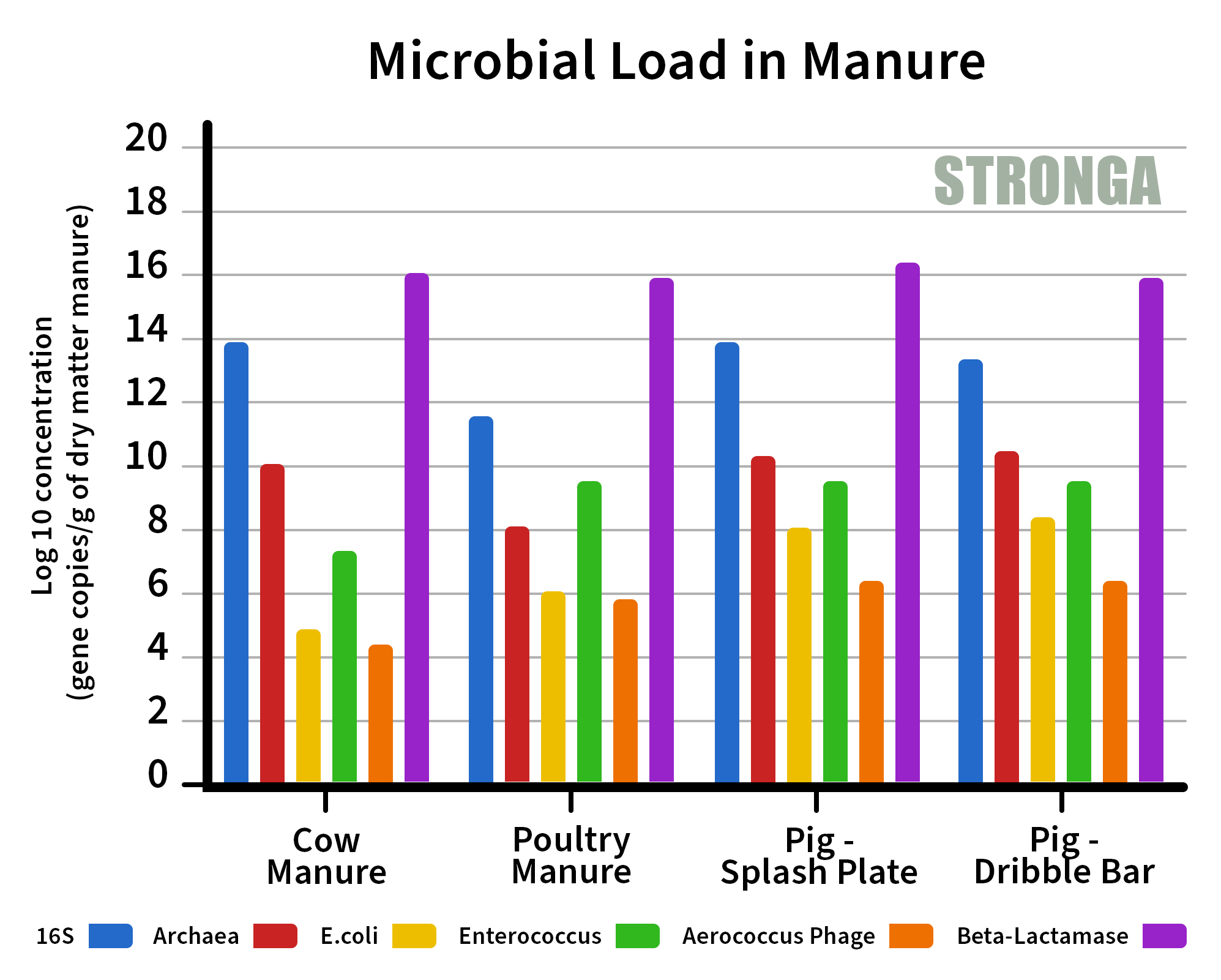
Stronga’s Batch Pasteurisation System Paves the Way Forwards
Stronga’s in-vessel steam pasteurisation system, FlowSteama Vessa, is capable of operating in either continuous or batch-mode to meet local standards for hygienisation. With adjustable ‘time-at-temperature’ settings, the Vessa model is capable of steam pasteurising a wide range of materials, including; livestock-derived manure, soil, separated digestate, anaerobic digestate fibre and various growing substrates. With an extremely high duty cycle and proven reliability in real-world applications – Stronga’s steam heat-treatment solution offers the best pasteurisation effectiveness available in the market.
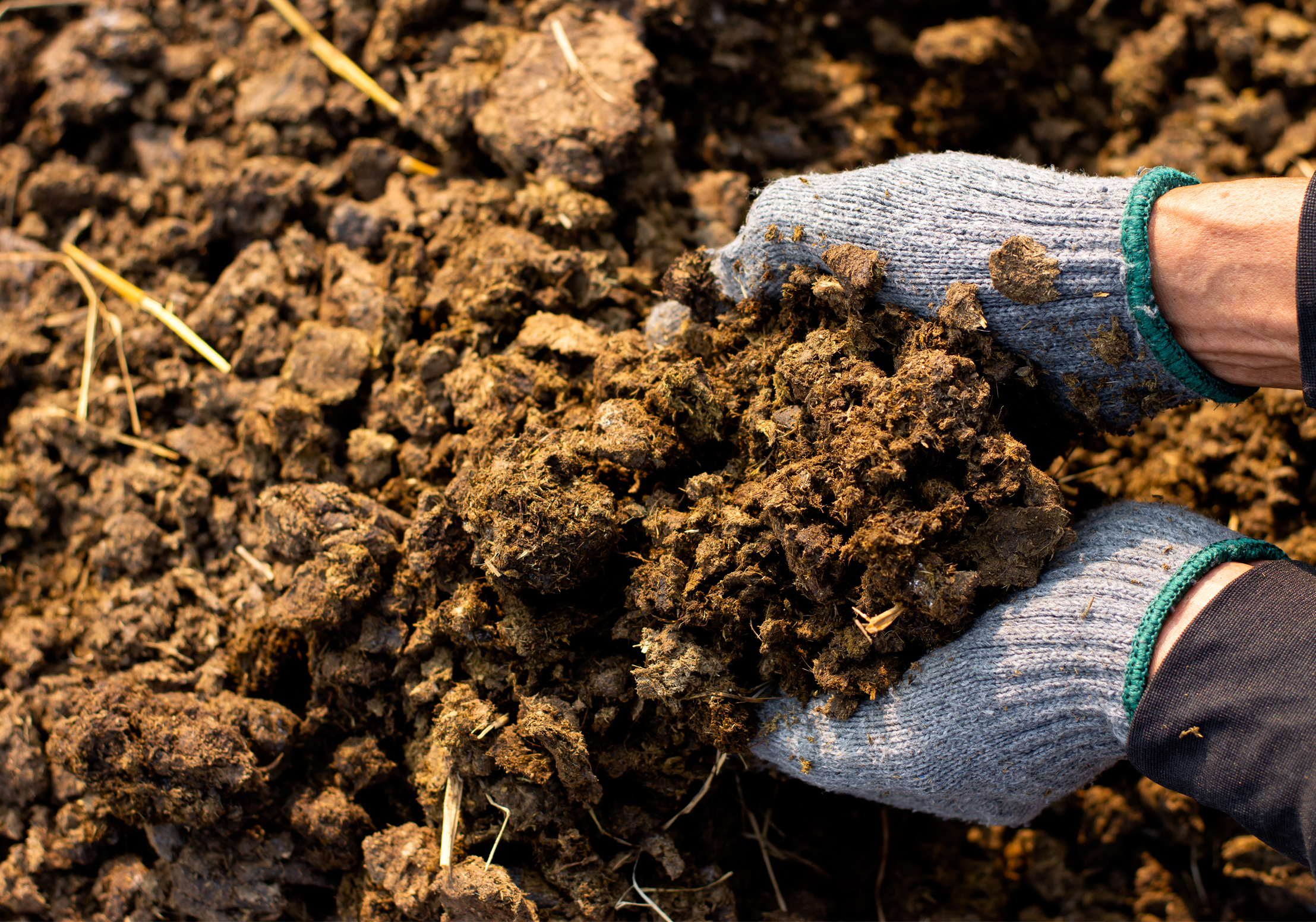
Steam pasteurisation with FlowSteama is highly efficient, allowing users to safely recycle used growing animal bed manures, digestate fibre and more, in an energy-effective process. The in-vessel steam process is productive and more likely to meet increasingly stringent government requirements compared to composting methods, which rely fully on management of microbial activity. FlowSteama is also far more cost-effective and environmentally-friendly than increasingly banned chemical sterilisation methods.
The FlowSteama system has an extremely low electrical requirement, with minimal labour hours required to operate the unit. What’s more, the design is simple and strong with very few moving parts; this enhances service life while minimising maintenance. FlowSteama Vessa, Stronga’s semi-transportable unit, offers high capacity and is one of the most economic and efficient pasteurisation systems available on the market.
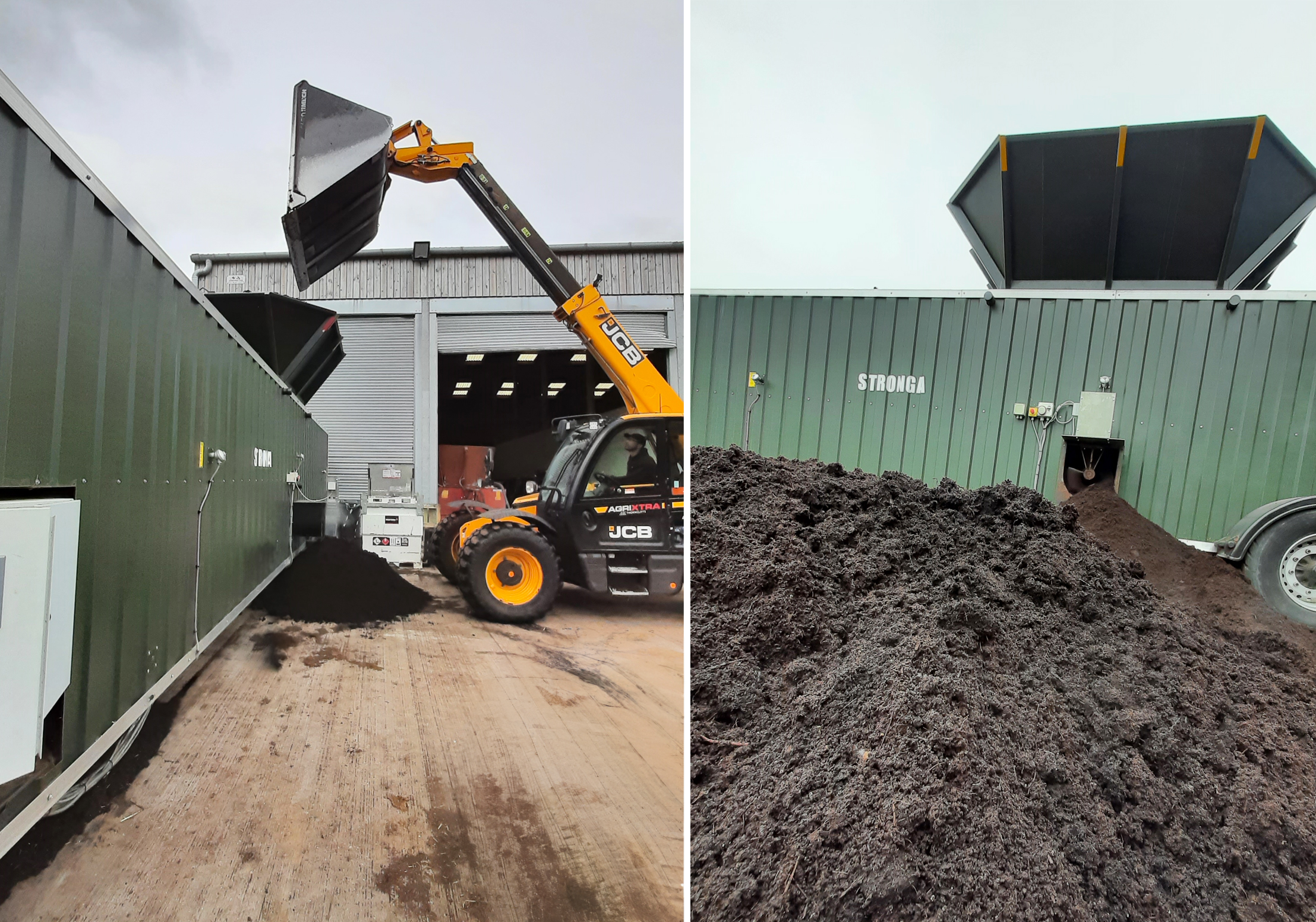
How Does FlowSteama Deliver Pasteurised Output?
When setup in ‘batch-mode’, the Vessa steam pasteurisation process from start to finish is as follows;
1. Unsterilized material (post anaerobic digestion fibre, cow/poultry manure or other blends) is loaded into the top infeed hopper on FlowSteama’s ‘dirty’ side. Once the hopper has been ‘plugged’ with dirty material, pasteurisation can begin.
2. Super-heated low-pressure steam (200’C) flows into the insulated, twin-tier vessel from the SteamBoila in an efficient energy exchange. Once the material becomes fully saturated with superheated steam, the SteamBoila automatically modulates down, minimising energy used.
3. As steam engulfs the vessel, it quickly and fully penetrates the material load which is agitated and mixed on both decks by the hydraulic ‘PulseWave™’ floor design. Once the batch is fully loaded, the process pauses for the programmed period to achieve the required ‘time-at-temperature’. Superheated steam remains in the vessel during the time-at-temperature batch process. The design of the FlowSteama ensures complete and rapid steam penetration of the material in the vessel. If digestate fibre is input for pasteurisation – the load can be pasteurised at a minimum of 70’C for the required duration.
4. During the pasteurisation period, the temperature logging function is operating, reporting via several sensors on the HMI and control system. FlowSteama’s smart, self-protecting logging systems allow operators to evidence and prove time-at-temperature parameters have been met – this is especially important when dealing with animal-derived by-products.
5. The pasteurised or ‘clean’ material self-empties from both moving floors in operation, discharging into the lower cross-feed auger on the ‘clean’ side. Heat-treated material can now be safely conveyed and stored in a suitable, clean-side store. With digestate fibre input, each batch’s output can be approximately 8 tonnes* – this figure depends on bulk density, initial moisture, particle size and other variables.
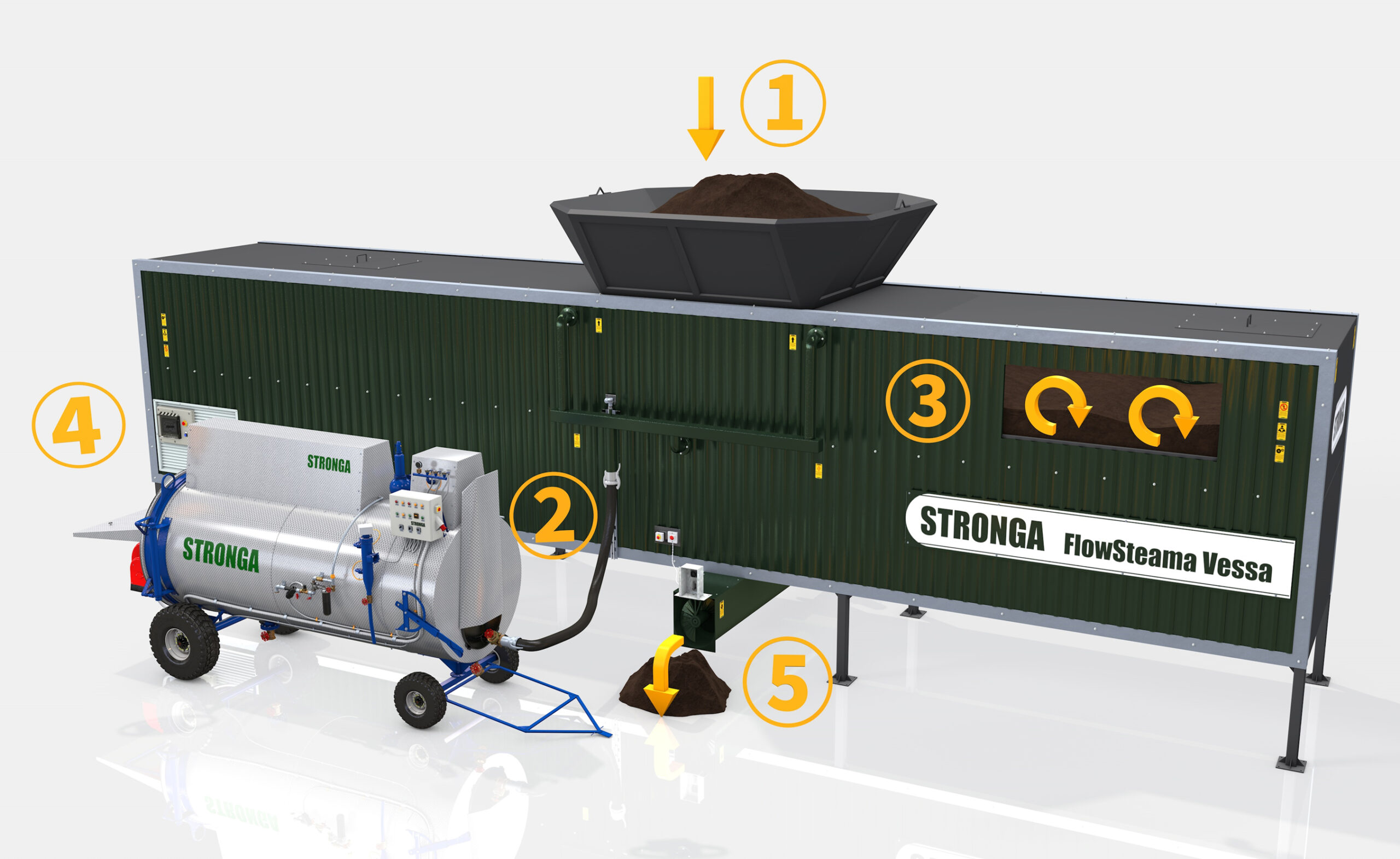
FlowSteama – Dependable & Reliable
Super-heated 200’C input steam generated by the Stronga SteamBoila removes weed seeds, viruses and pathogens during the FlowSteama batch process, whilst also accelerating composting processes. The unit is designed to be as simple and effective as possible; there are no belts, conveyors or chains which are generally subject to high service and maintenance costs.
FlowSteama can be configured by the operator to pasteurise substrates and fibres at required parameters on a batch operation basis. The overall hygienisation process is monitored via temperature probes positioned in strategic points in the vessel including input point (dirty-side hopper) and steam input temperatures, both tier decks (mid-flow) and exit auger point (clean-side discharge auger).
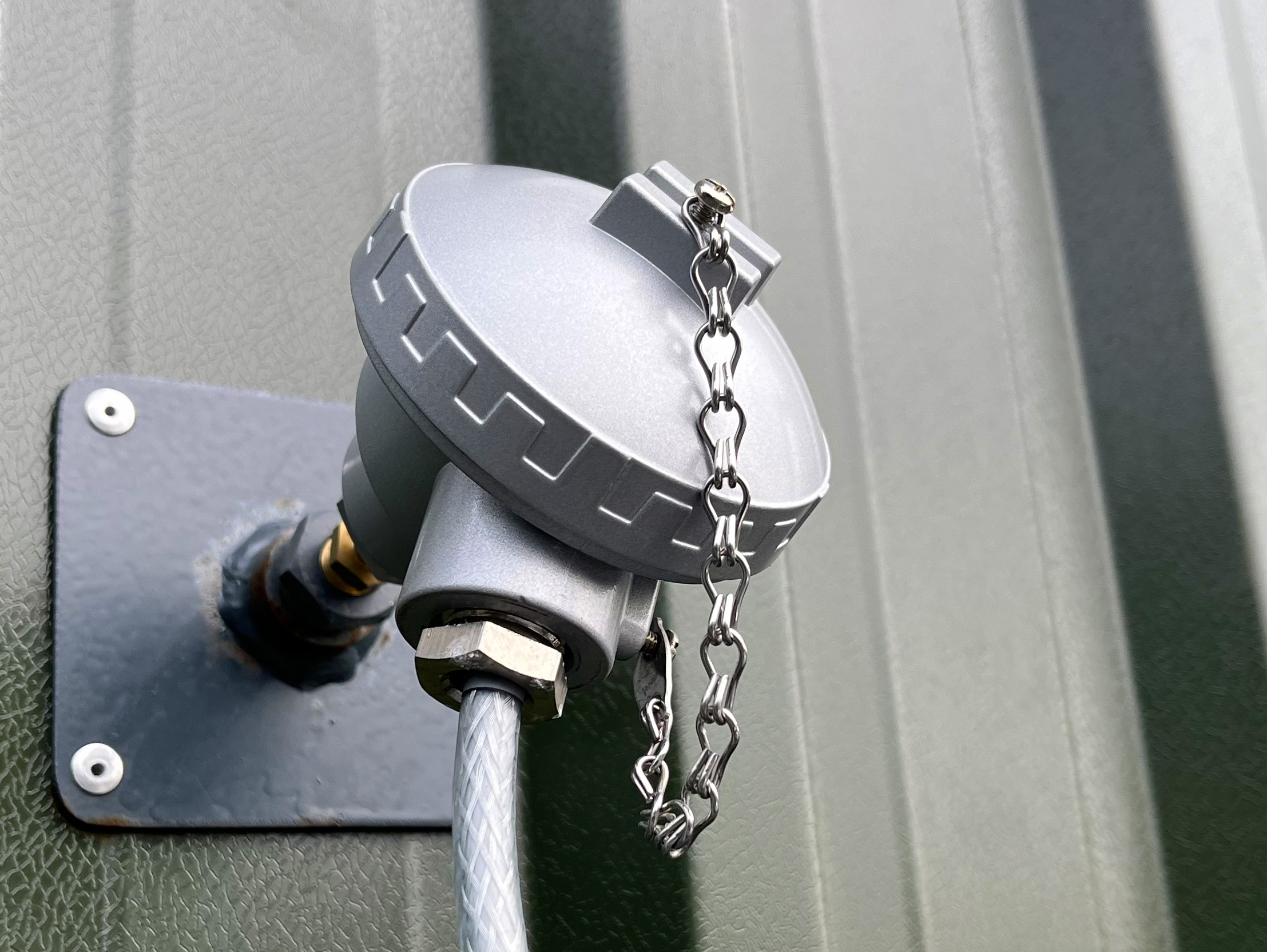
The logging functionality enables an audit trail, allowing FlowSteama owners to comply with the strictest modern protocols, typically in place for sites pasteurising digestate fibre from animal by-products. These accurate recordings prove material has reached the required temperature for pasteurisation compliance and, importantly, has remained at temperature for the required residency time, an essential requirement for most regulations. These certifications demonstrate regulation compliance and reduced risk of disease transmission. They are also important for onward sale of the pasteurised material (compost/soil enhancers etc.), increasing their value.
FlowSteama control software is self-protecting and operable in both automatic and manual modes. All control features are accessible via the SteamStation™ HMI and each batch report is available for up to a year after the process has been completed. Only authorised operators can adjust parameters, while batch pasteurisation thermograph data is recorded in real-time. These data logging features enable optimised batch output efficiency and evidence of pasteurisation.
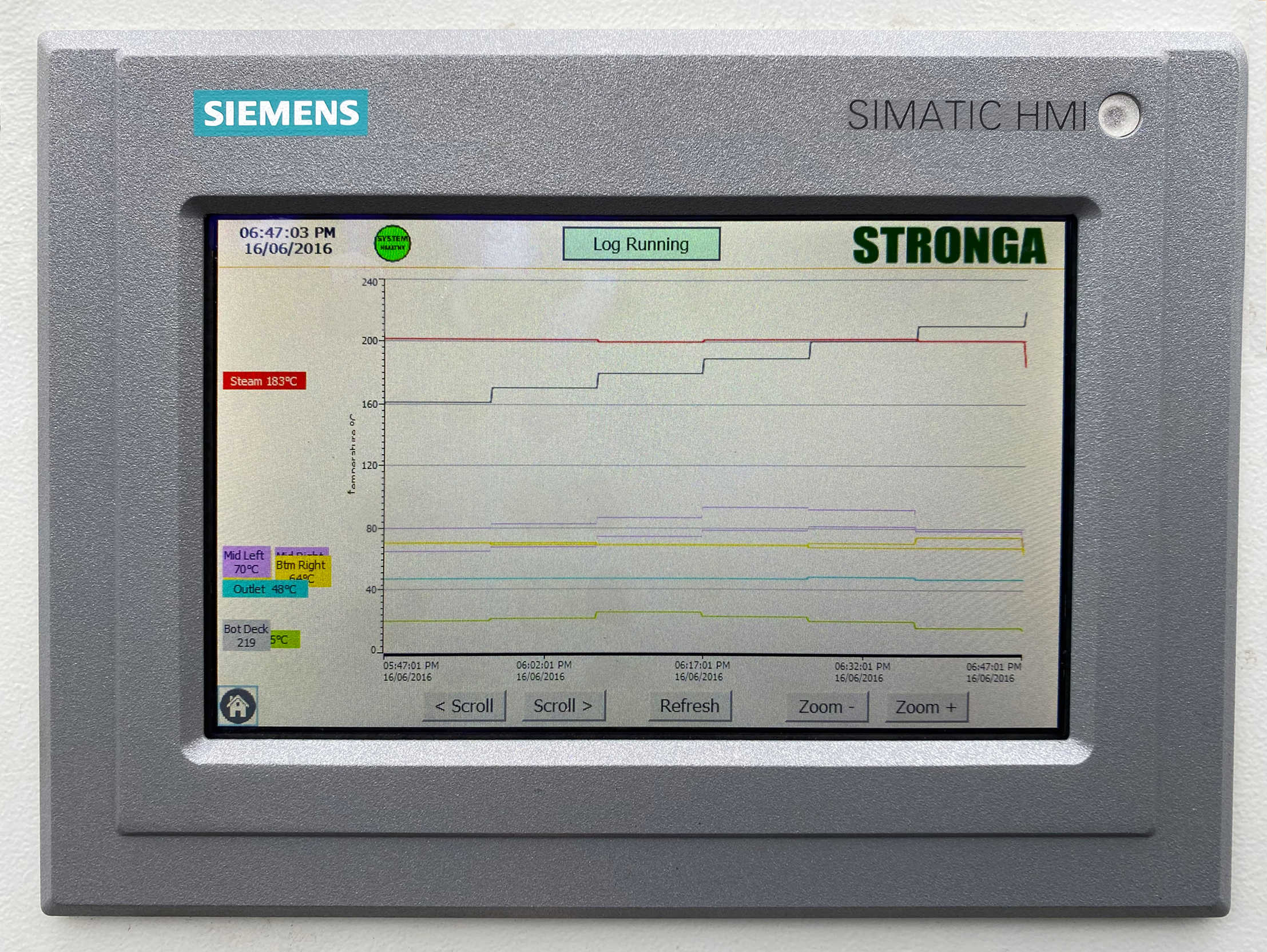
FlowSteama’s in-vessel pasteurisation system aligns with relevant safety requirements. Despite the well-proven, tried and tested design which features clear ‘dirty’ and ‘clean’ zones, FlowSteama operators must be aware of conveyor or bucket sanitation when collecting and transporting dirty/clean material streams. It is essential that sterile equipment is used when transporting and storing the pasteurised material, otherwise there is a risk of cross or re-contamination. FlowSteama’s optional auguring systems allow for easy stockpile set ups which reduces handling and contamination risks – but these will also need to be sterile and separate from one another.
FlowSteama is well equipped with E-stop shutdown capabilities in the unlikely event of disruption to operation. For more information on any of these security functions, please get in touch with our team at info@stronga.co.uk

FlowSteama’s pasteurisation systems enables circular growing opportunities, reduced waste and enhanced usage of digestate fibre (animal by-product) materials. Pathogen-free output material can be used or sold as a valuable asset which reduces the need for chemical fertilisers or manual composting processes. For more detailed information regarding digestate fibre batch pasteurisation, please get in touch with the Stronga team - info@stronga.co.uk
Share this post