The Value of Good Tree & Bark Health
Trees are precious natural resources that sustain life in all forms. They are vital economic, environmental and social assets. They contribute to food supply, capture carbon, reduce noise pollution, prevent flooding and are essential to biodiversity. Trees shape and beautify the landscape, support wildlife, provide timber and support our health and wellbeing.
However, the threat to tree and tree bark health from pests and disease is real and increasing. Globalisation of travel and trade and demands for a greater variety of plant species mean threats are now ever-present as we have access to new sources where different pest and disease threats may occur.
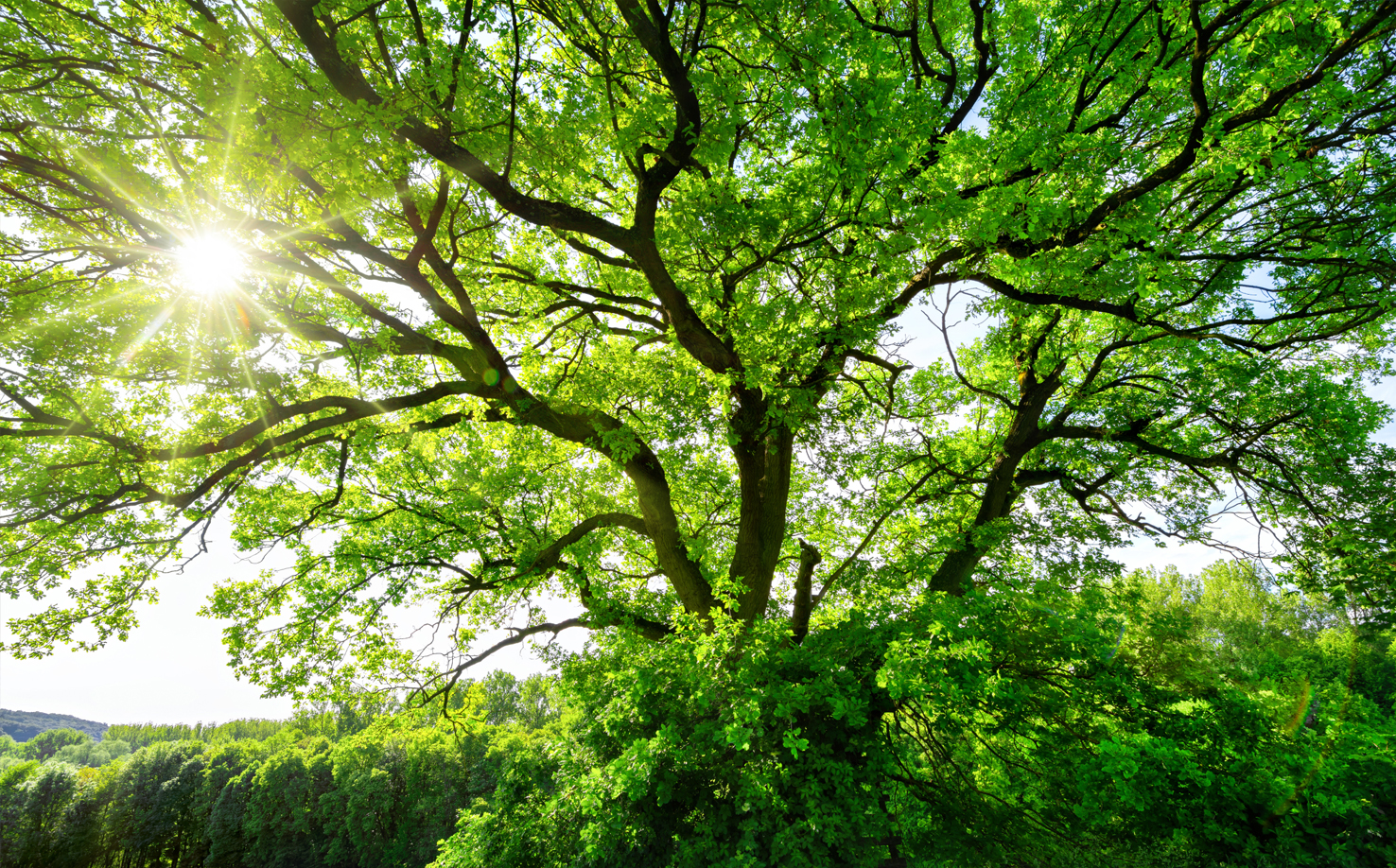
Improving Biosecurity Practices
Rules and regulations applied by local governments are becoming increasing tough in order to reduce the risk of importing or exporting pest and disease threats. While the challenges from potential threats like Xylella and Emerald Ash Borer are real, the regulations put in place now and in the future will protect trees and bark products.
It is the responsibility of forestry, landowners, environmental and conservation organisations to put in place the right processes to ensure long term tree and bark health resilience.
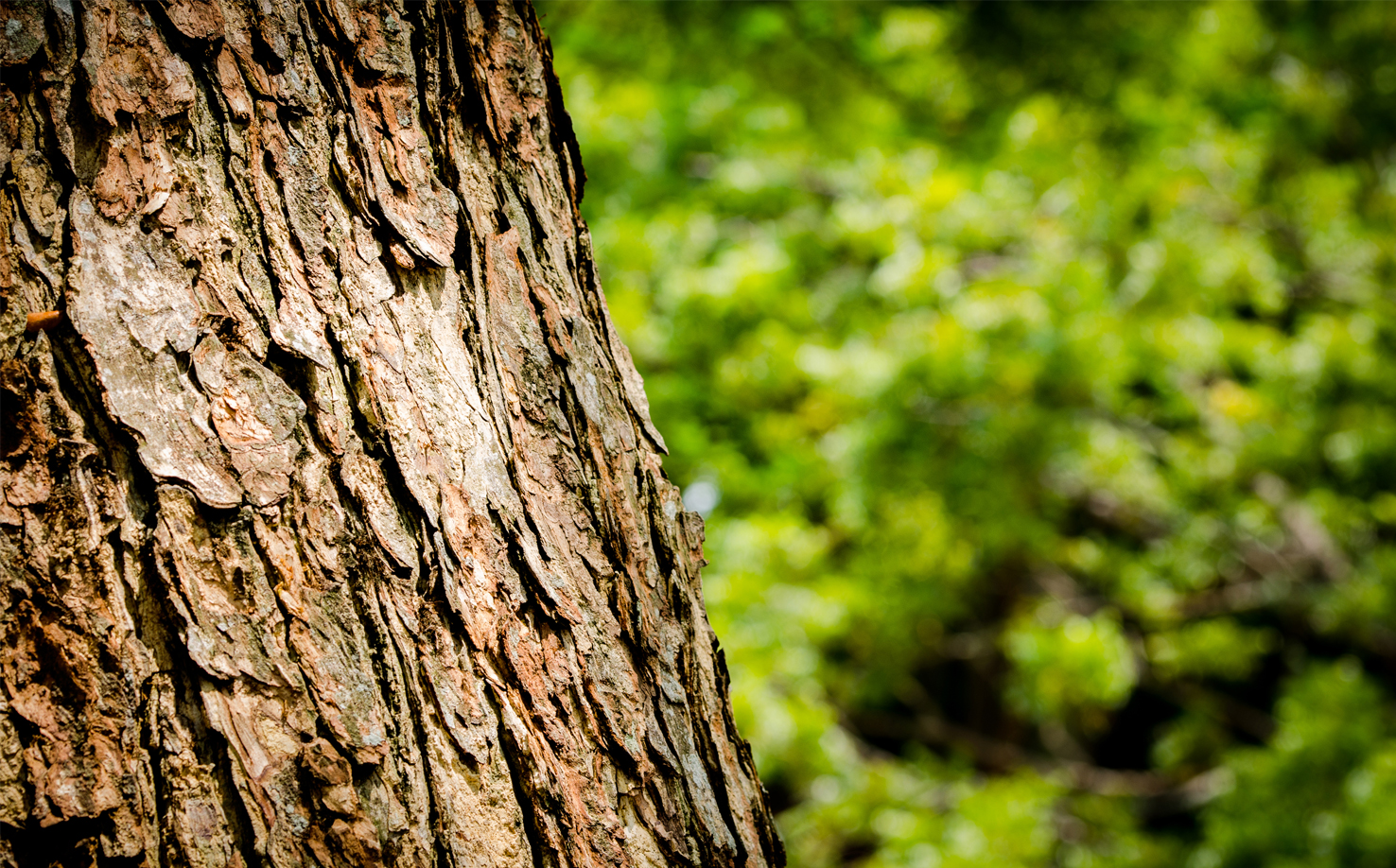
In-Vessel Heat Treatment
Forestry, environmental and conservation organisations are increasingly turning to in-vessel heat treatment as a highly efficient, effective and environmentally-sound means of steam sterilising tree bark into biosecure, heat-treated, sanitised stockpiles, free from pests and disease.
A key benefit of the FlowSteama from Stronga is the ability to create an audit trail and keep record of the biosecurity measures put in place; this practice is not yet employed holistically but will soon become mandatory as tree health regulations come to the fore.
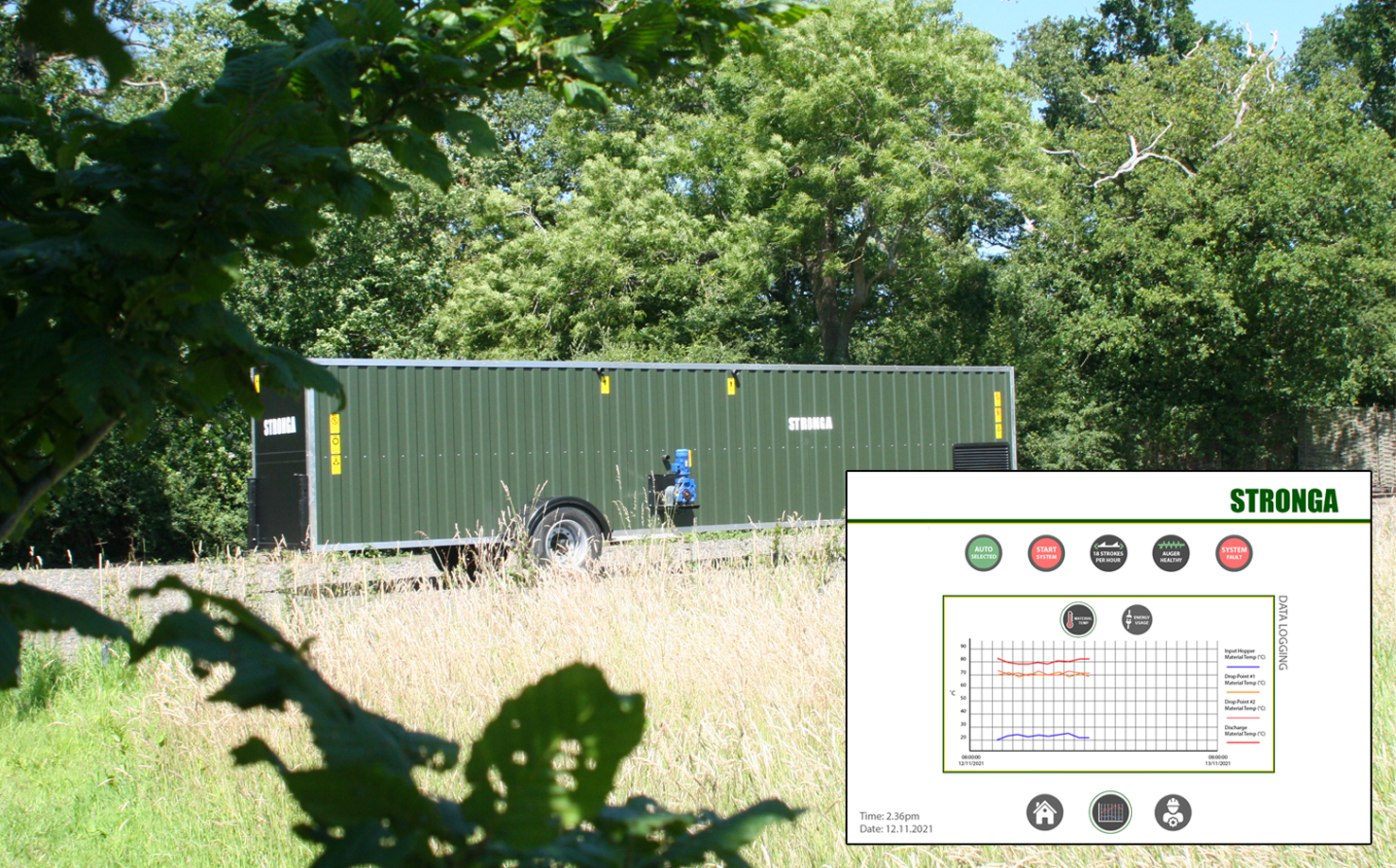
FlowSteama Rova
Stronga produce two types of in-vessel heat treatment system – FlowSteama Vessa and FlowSteama Rova. Unlike the Vessa model, the FlowSteama Rova shown in the video can be easily moved on-site between stockpiles of bark mulch substrates, and also between adjacent sites, enabling smaller commercial companies to share one Rova between them.
When coupled with SteamBoila - Stronga’s mobile, low-pressure super-heated steam generator, suitable water supply and fuel source, FlowSteama Rova can be located adjacent to bark stockpiles for hours, days or longer, depending on the client’s biosecurity and hygienisation requirements. The extract below details the videoed bark heat treatment process in more detail.
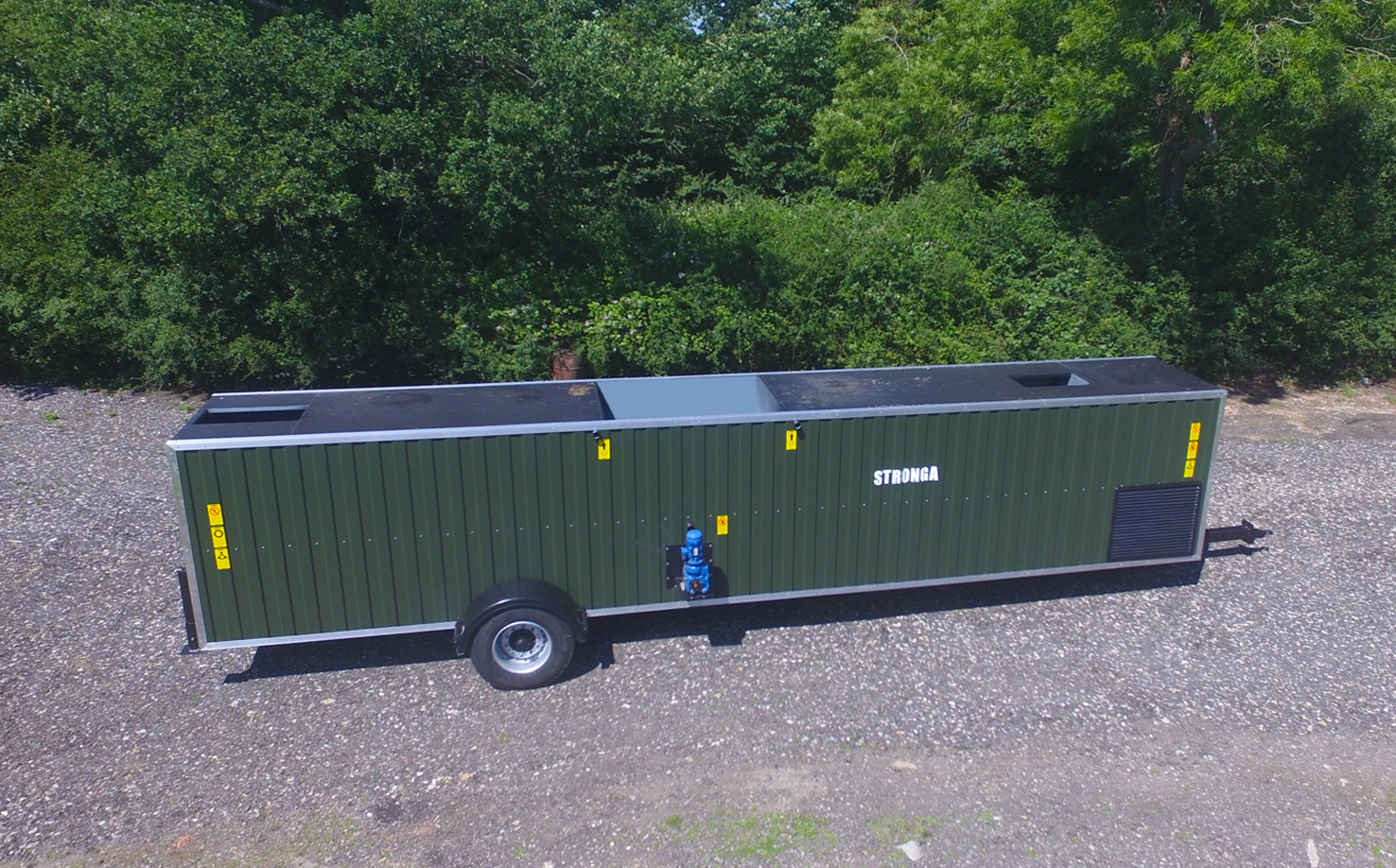
Screened-Down Bark Product
The material shown in the video below is a screened-down bark product sourced from a sawmill. The heat treatment site was organised to avoid cross contamination of the bark mulch material between the unsterilised “dirty” and steam sterilised “clean” side. Two separate loaders and buckets were used and bark product stockpiles were clearly separated to ensure optimum biosecurity practice.
A key feature of the FlowSteama Rova is the temperature sensors which probe the material temperature profile during the bark heat treatment process. These sensors are connected to time-logging PLC which records the sensor output signal over time and logs results in real time. There are output logs of temperature and time, allowing operatives to evidence material temperature and residency time in order to demonstrate that the bark heat treatment process has been completed to regulations.
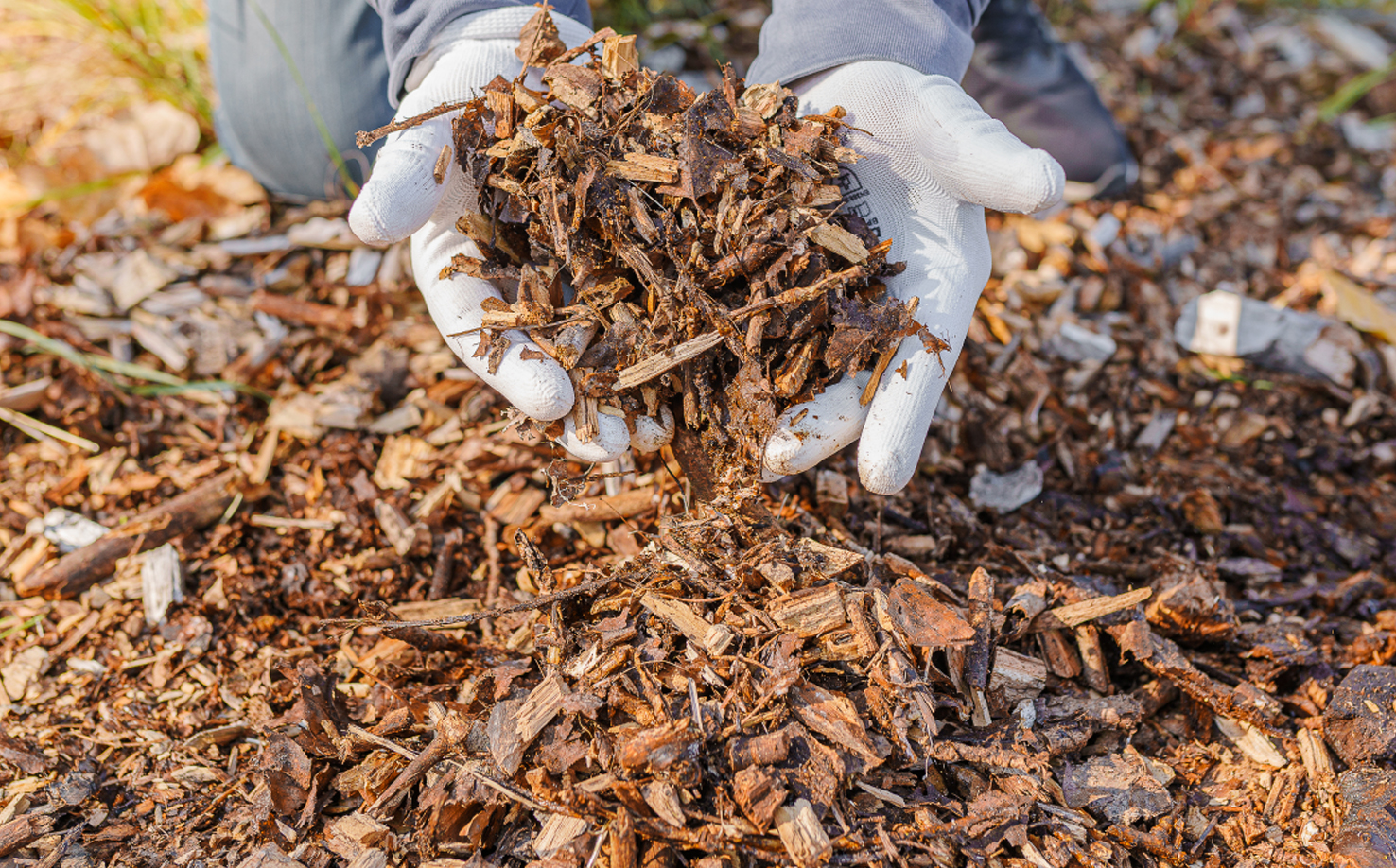
Heat-Treating Medium Grade Bark
In the first stage of the heat treatment process, the FlowSteama in-vessel system is charged with steam so the machine is pre-heated to temperature prior to bark mulch material being loaded. Steam rapidly raises the temperature of the medium grade bark material it comes into contact with.
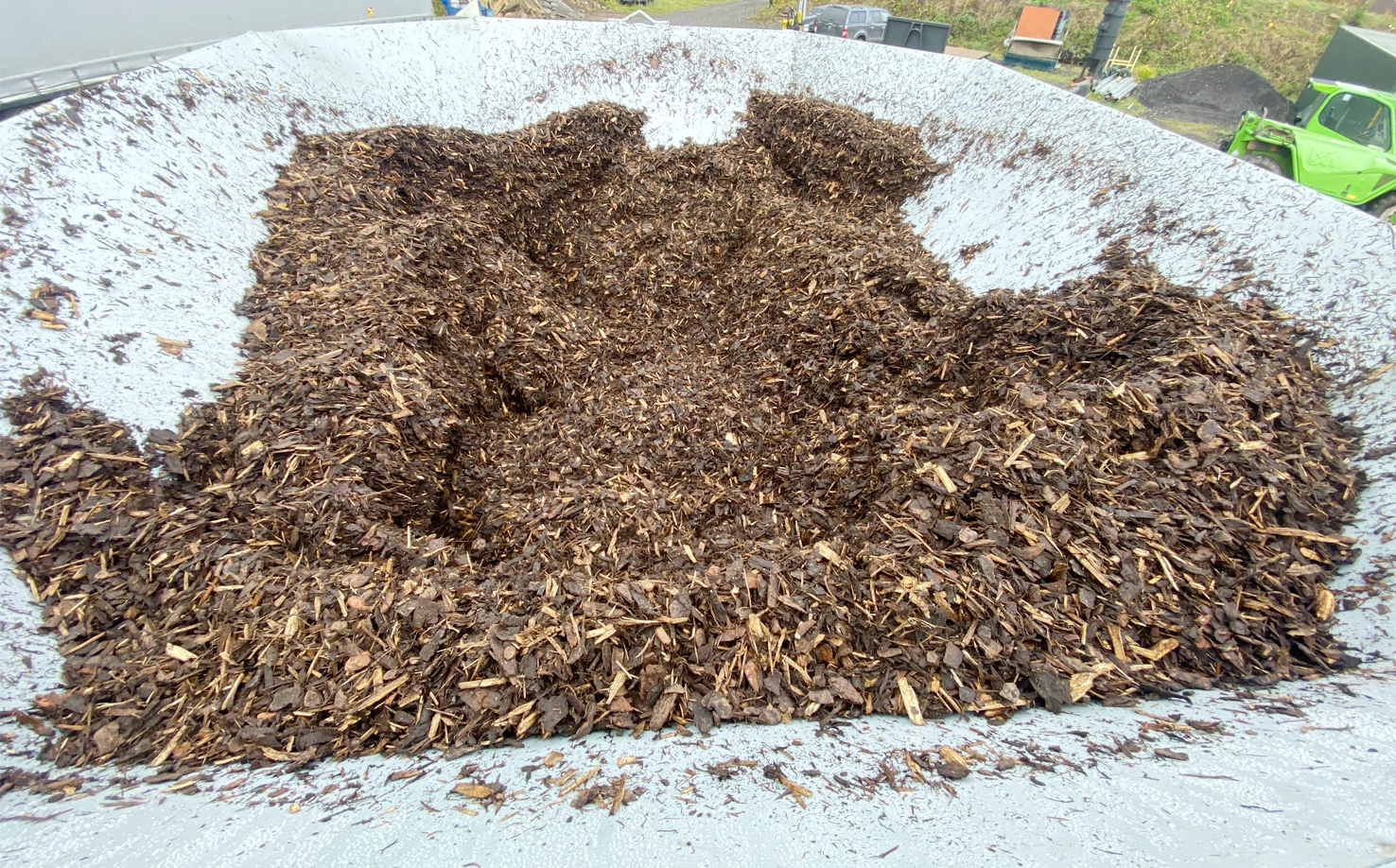
From the central loading hopper, the top deck hydraulic moving floor moves the bark mulch towards both ends of the machine. The top deck is designed to be shallow to allow optimal steam penetration of the medium grade bark. The floor is designed to create a wave of material during the moving floor cycle, thus the material is agitated, tumbled and mixed to allow rapid and full steam penetration.
The FlowSteama Rova is double-skinned and insulated to preserve operating steam temperature and reduce energy losses. The floor and inside sides are stainless steel which conducts heat directly into the material.
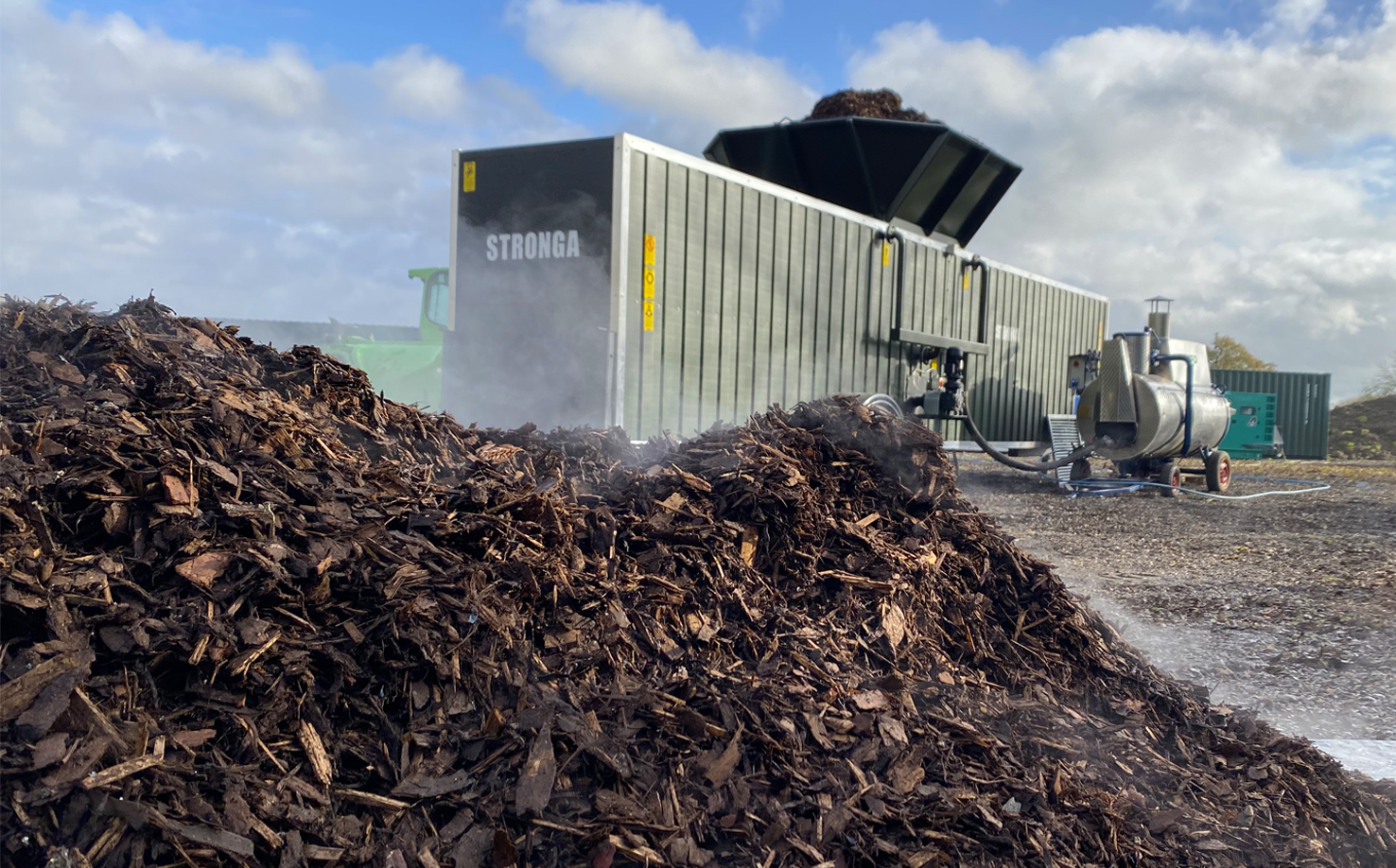
Each deck has a steam feed pipe system sized to evenly distribute the 550kg of steam per hour. Once the bark mulch reaches the end of the top deck moving floor, it drops though the steam-filled chamber onto the bottom deck. This dropping process is designed to allow further full steam penetration into the treated bark.
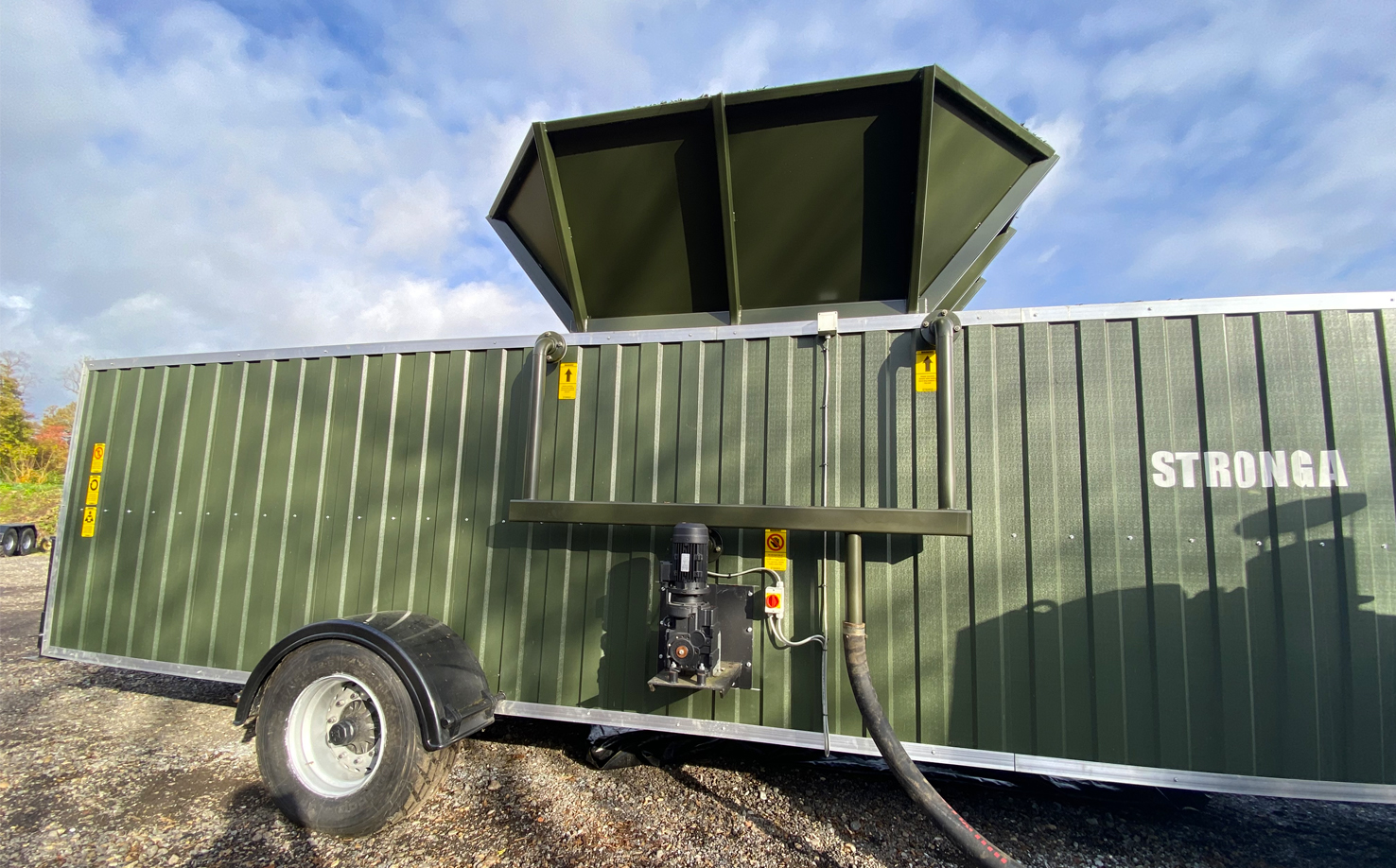
Bottom Steaming Deck – PulseWave™ Agitation
The bottom steam deck is longer than the top. The material is designed to be deeper on the bottom deck and is continuously agitated when the FlowSteama is set to continuous mode. Floor stokes per hour can be adjusted from continuous stroking via the HMI touchscreen in order to reach the client’s desired steaming residency time.
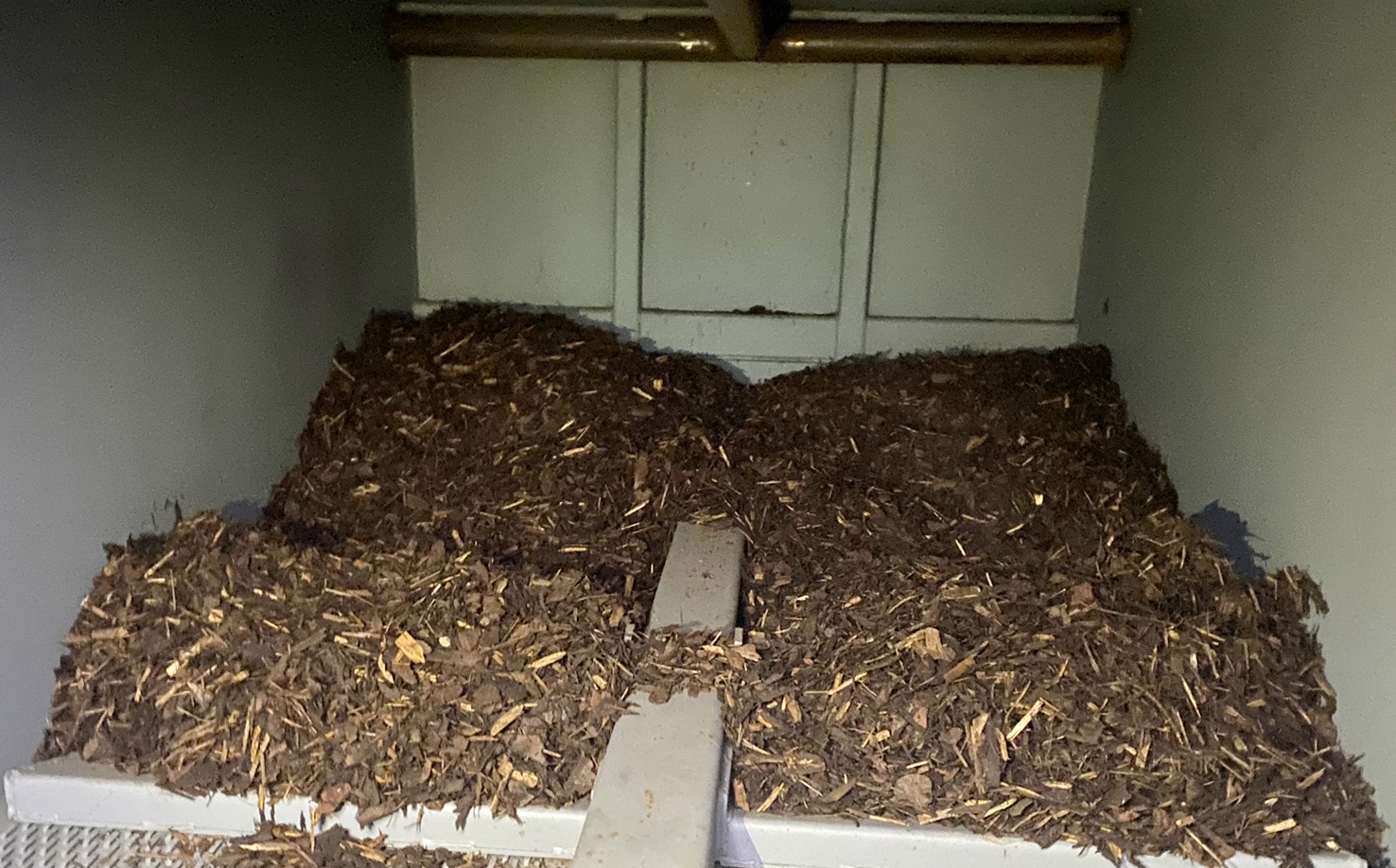
In this particular case study, the sensors at both dropping zones on the lower deck recorded that the medium bark mulch had reached a temperature of 65-75˚C after the initial top deck steaming period. A further sensor at the discharge end of the bottom deck recorded 75-85˚C material temperature. Based on the set floor speed, the client is able to evidence that the bark mulch was treated above the required 56˚C for a time period far exceeding the required 30 minutes. The output material was placed into a clean side loader bucket and conveyed to the sterilised stockpile.
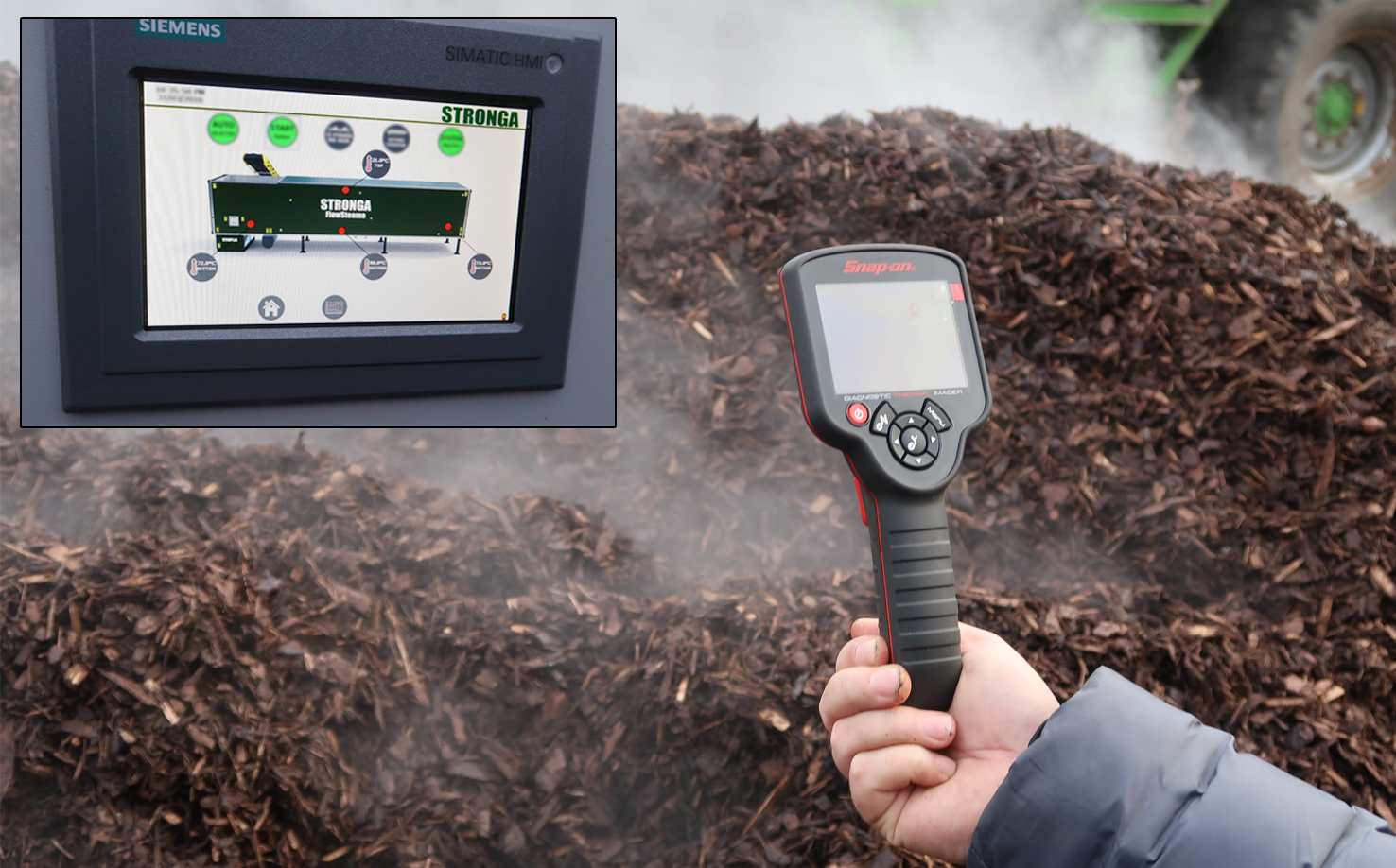
FlowSteama vs. Other Heat Treatment Methods
Stronga believe that other methods of hygienising bark products and other organic materials are simply not reliable when compared to the FlowSteama process. The outer layer in wind rowing, for example, never reaches the required temperature, whereas the FlowSteama can achieve this with evidence via the HMI touchscreen data logging function.
If you would like to discuss bark mulch heat treatment in more detail, please feel free to contact Stronga today to discuss your project. We look forward to hearing from you – info@stronga.co.uk.
Share this post