Heat Treating Growing Media Blends
Stronga recently coordinated a steam heat treatment trial on behalf of a client in the UK who is seeking suitable alternative growing media solutions to peat which is gradually being phased out from usage, sale and import. The material tested in the steam heat treatment trial was fine grade bark mulch sourced from a British sawmill. FlowSteama can be utilised to efficiently and economically heat treat a wide range of growing media blends, composts, topsoil’s, soil improvers and more.
The purpose of this article is to discuss modern-day peat extraction, the regulations preventing the use of peat usage in the future, and the alternative solutions available to commercial growers. All of these points will be discussed in relation to Stronga’s FlowSteama heat treatment solutions.
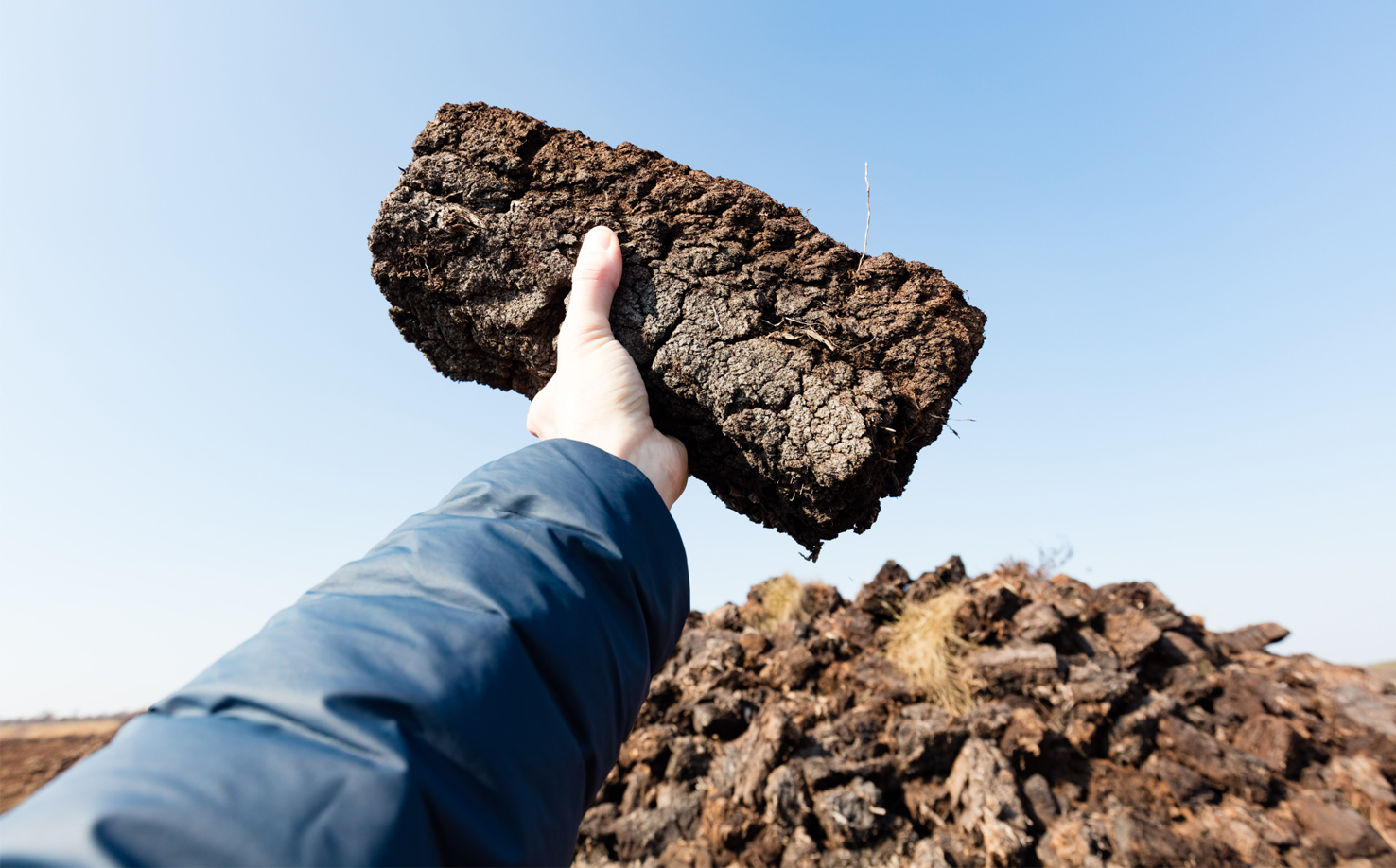
Transitioning Towards Peat-Free Horticulture
The government in the United Kingdom has increasingly pressed for significant reductions in the quantity of peat used for commercial and domestic horticultural purposes. There are significant targets in place to transition towards peat-free horticulture. These targets include the eradication of peat usage by amateur gardeners and commercial growers by 2030 with the view to protecting the natural environment and reducing greenhouse gas emissions.
With government regulation on peat extraction and usage coming to the fore, change is on the horizon. Horticultural organisations are increasingly looking to alternative sources for use in their growing operations. The graphic below shows a timeline of key events in the transition towards peat-free media.
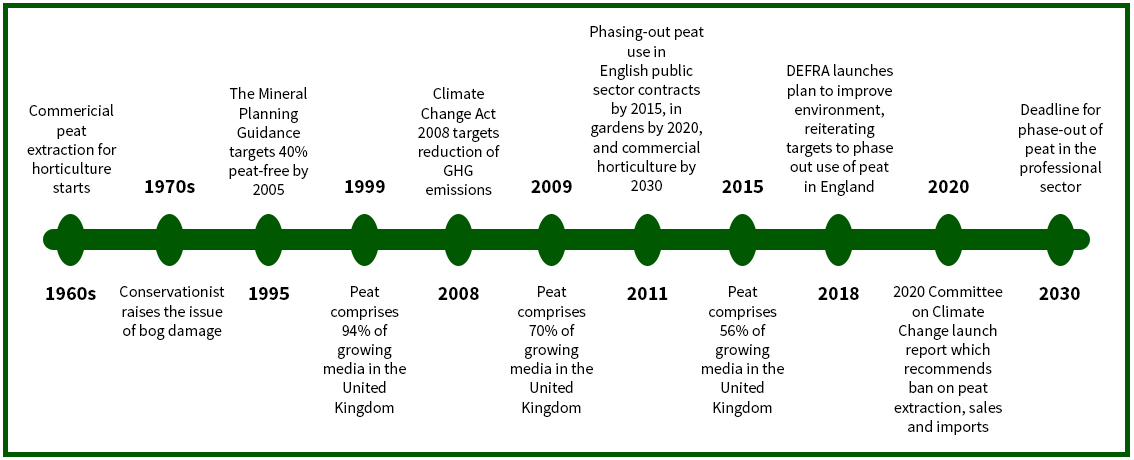
Issues with Peat Extraction
There are currently no new planning permissions being granted in the UK for peat extraction. Imported peat costs are reaching extremely high levels while there are added fuel costs, CO₂ and hydrocarbon elements of shipping peat from overseas regions like the Baltic States. Peat is subject to “the tragedy of the commons” whereby the resource, which is a wonderful but limited natural resource for growing food, has been and is still being over extracted. The time has come where the level of peat extraction is entirely unsustainable.
• Peat is non-renewable – it will run out.
• Peat is created extremely slowly over 1000s of years.
• Peat bogs are a huge store of atmospheric carbon – far greater than trees.
• Peat bogs support unique wildlife habitats that are destroyed in some unmanaged situations.
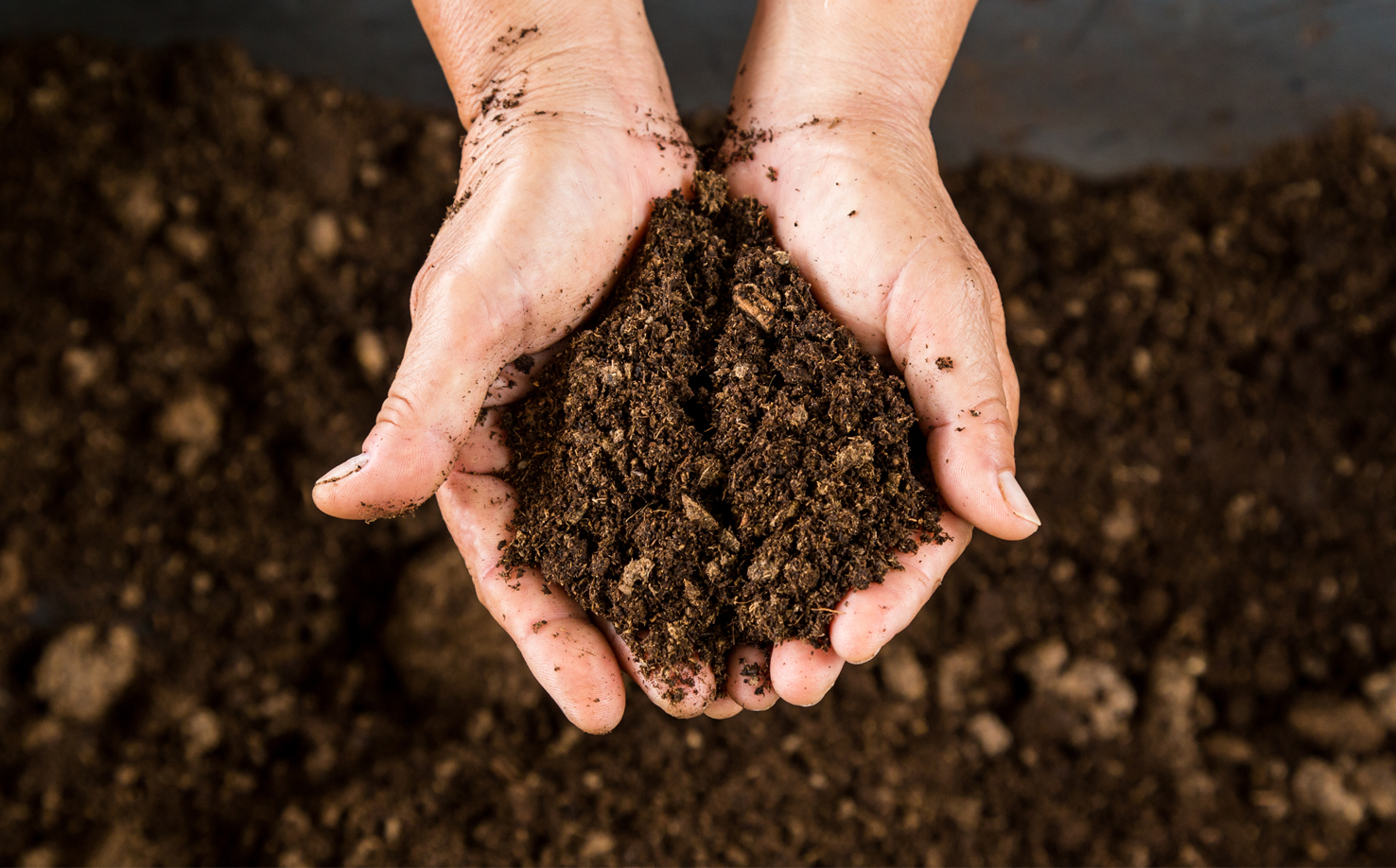
Alternative Growing Media Solutions
Weed burdened topsoil’s from development and construction sites are currently being sent to landfill or otherwise buried. This is a tremendously irresponsible waste of limited and valuable topsoil which takes 1000s of years to form.
On building sites, stripped topsoil’s become mixed and contaminated. Blending these stripped soils with soil improvers can increase the physical and/or chemical characteristics of the product; however weed burden and pathogens are highly likely to be present in the material. There is therefore a need for the employment of a suitable heat treatment solution in order to produce a quality, sanitised growing medium, free from plant pathogens, pests and weed seeds.
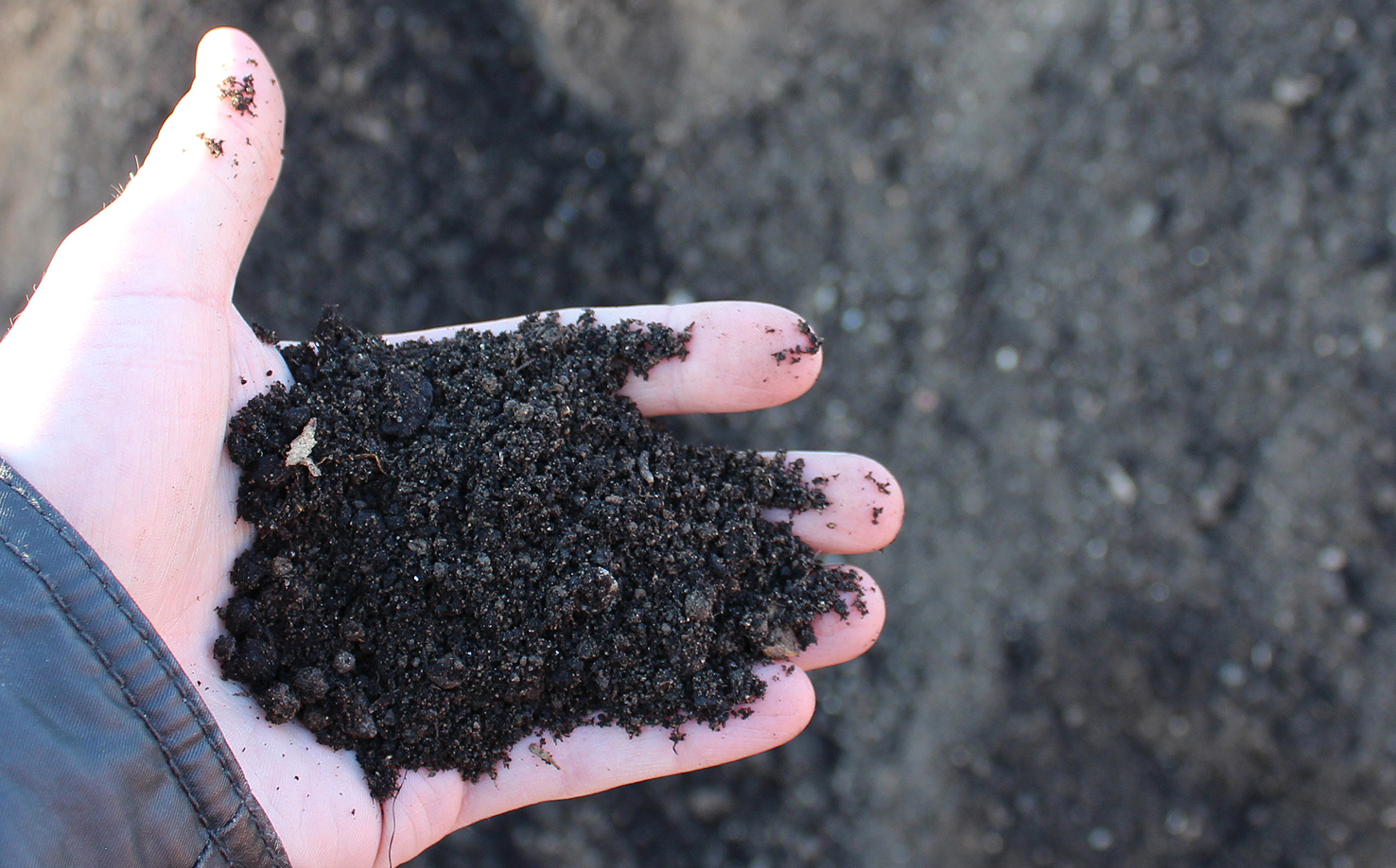
The Stronga Solution
Stronga produce a mobile, low cost per m³, heat treatment solution designed to efficiently clean weed-burdened topsoil’s, composts, bark products and growing media blends. The Stronga solution is called FlowSteama Rova. By heat treating the soil blend locally using modular, mobile FlowSteama Rova equipment, the handling and CO₂ costs of moving heavy soil are massively reduced. Other benefits of FlowSteama include:
Straightforward assembly on-site ✓; plug and play heat treatment system ✓; no use of harmful chemical sterilisation techniques ✓; ability to create an audit trail and keep record of biosecurity measures ✓; full control of heat treatment residency time ✓; fully insulated, thermally efficient design ✓; and much more.
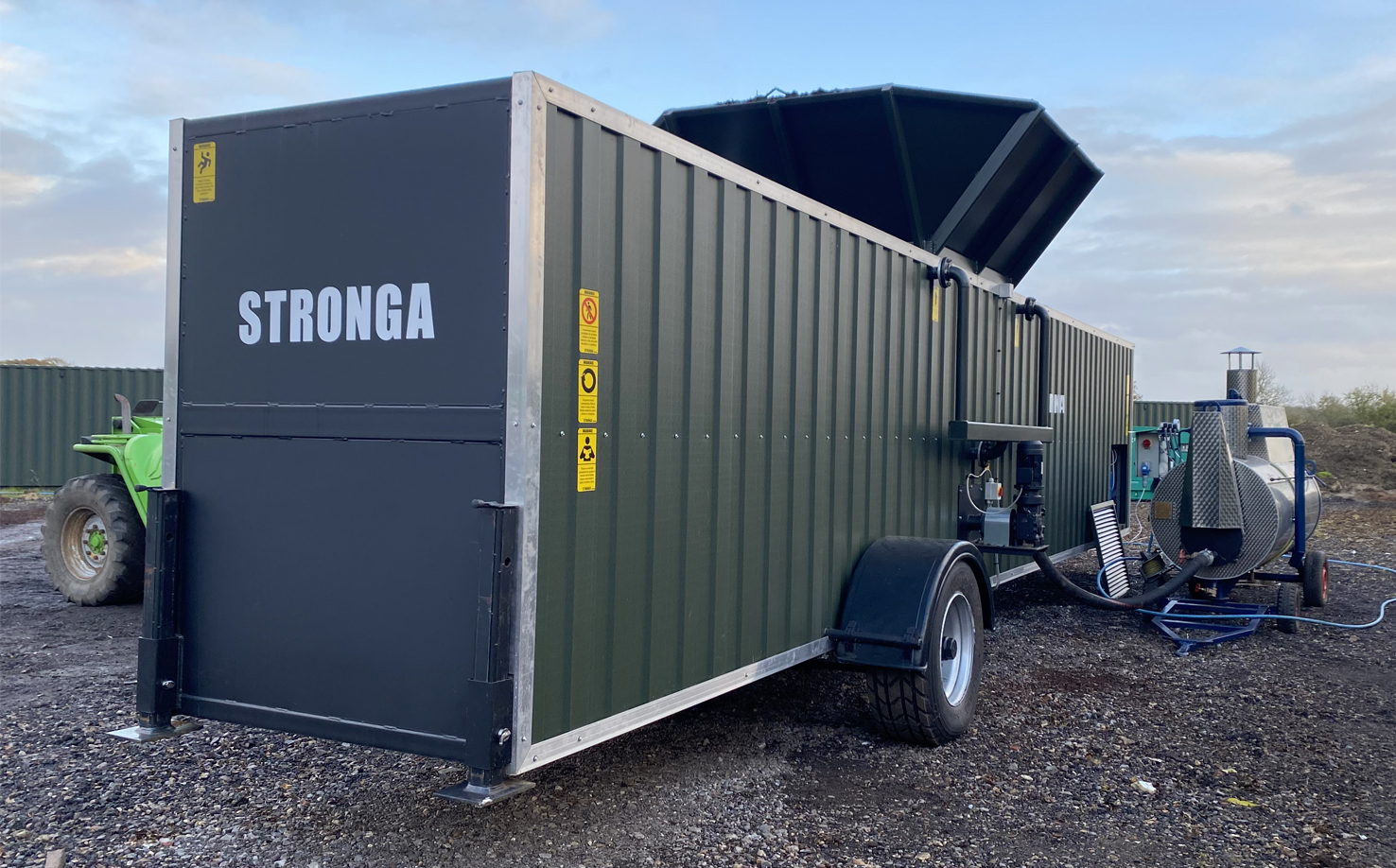
Fine Bark Heat Treatment
The following section of the article presents a basic overview of the findings from Stronga’s recent fine bark heat treatment trial. If you have any questions or would simply like more information, please feel free to contact Stronga today to discuss the trial further – info@stronga.co.uk.
Watch footage from the steam heat treatment trial day below.
In the first stage of the steam heat treatment trial, a sample of the fine bark mulch material was oven dried to determine the moisture content immediately prior to the steam heat treatment. The initial weight of a known volume was recorded and then the weight was measured over the drying cycle at regular time intervals until no further loss of weight was recorded. Temperature was monitored during the process to ensure the temperature did not exceed limits where loss of material would occur.
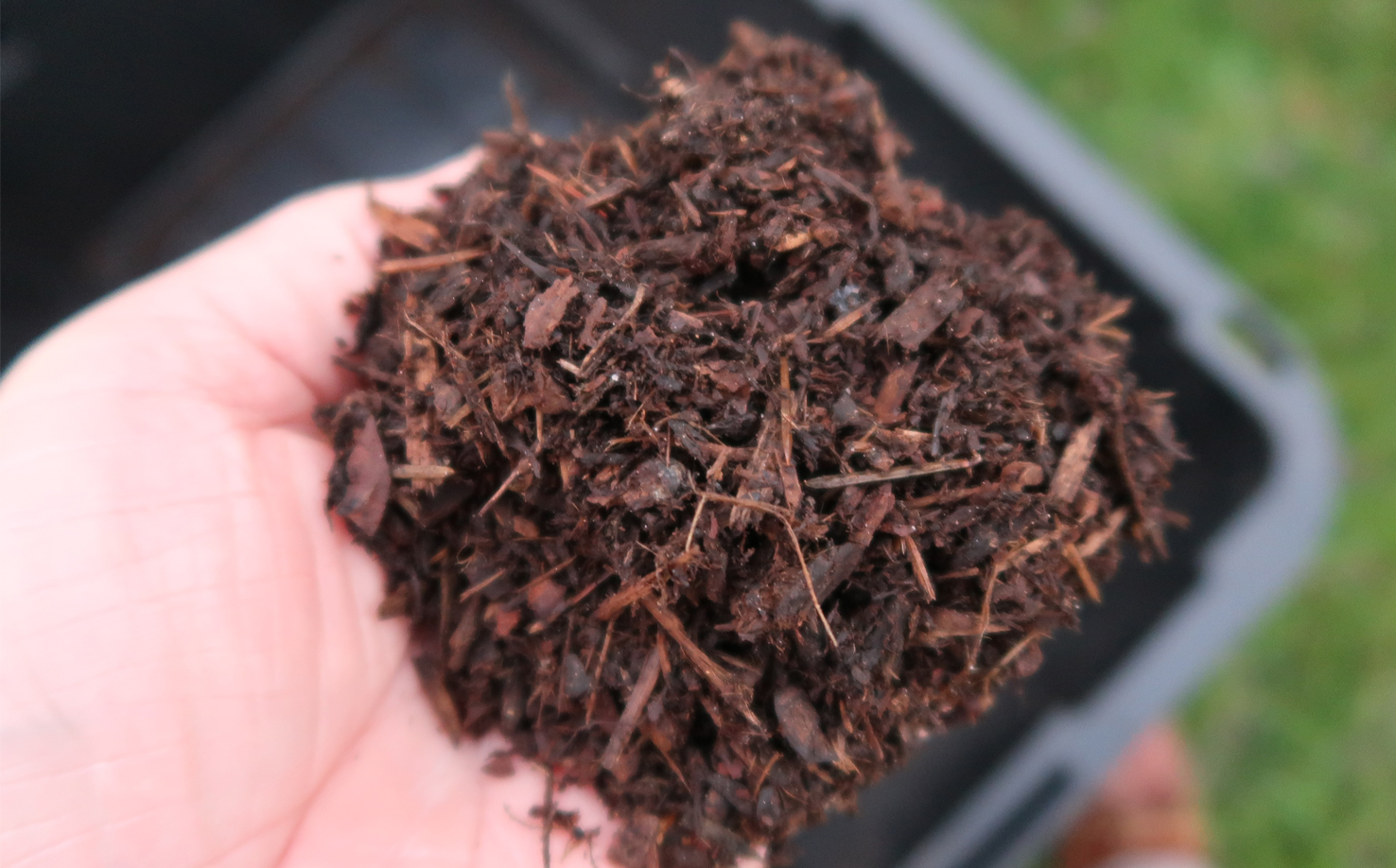
Material temperatures were checked using both a thermal camera and IR heat thermometer during the heat treatment trial. The outside of the unsterilised stockpile was close to ambient temperature while the inside of the pile was recorded at 22-25˚C due to thermophilic activity.
During the heat treatment process, the 200˚C super-heated steam from the SteamBoila heated the fines material incredibly efficiently. The temperature at the cross auger discharge point of the fine bark always exceeded 75˚C while the maximum recorded temperature at this same point was 85˚C. The outer layer of the bark material cooled rapidly as steam was vented, however the material held temperature at a high level for a very long time, as the video shows.
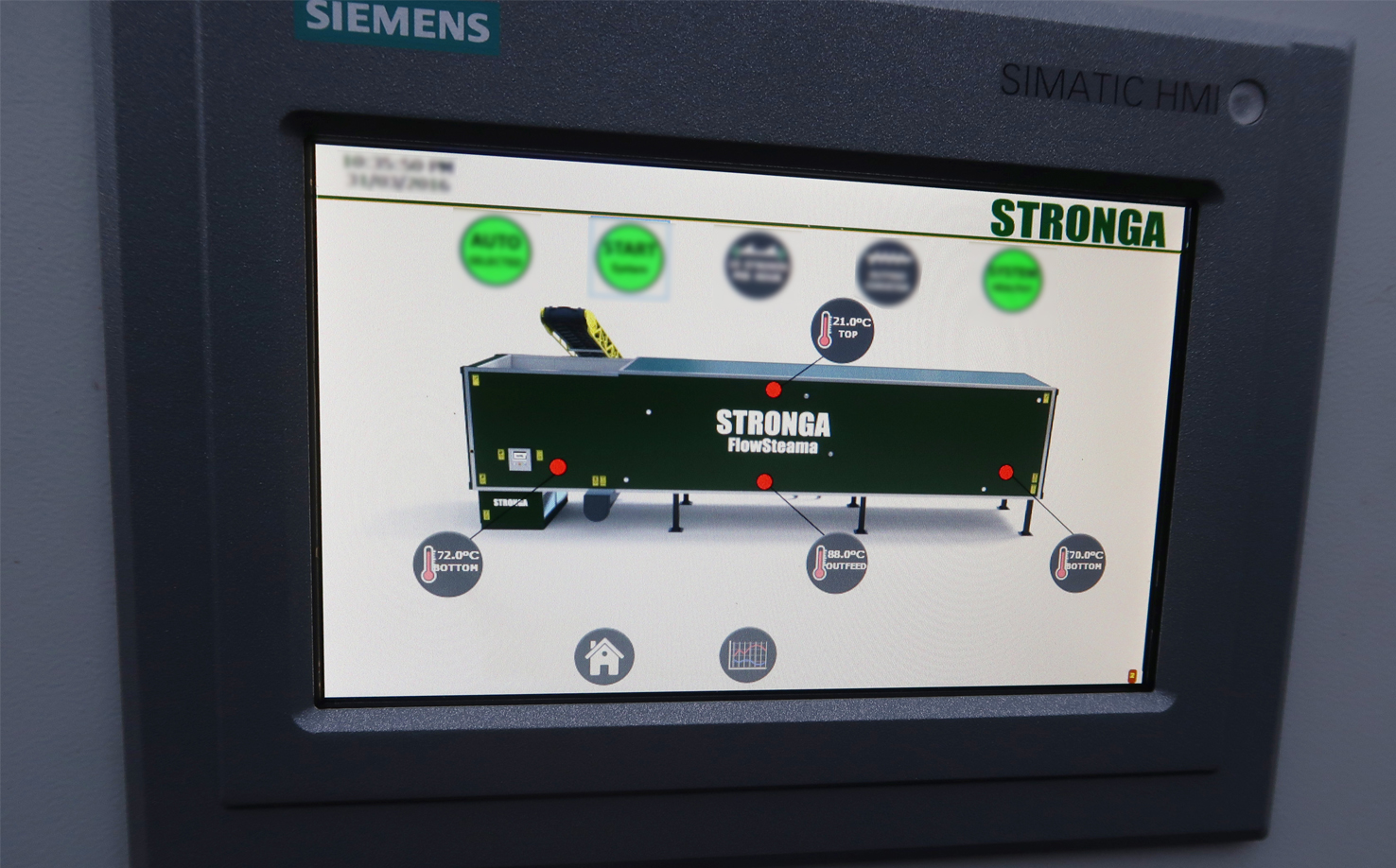
At the end of the steam heat treatment process, the sanitised fine grade bark output was placed into a “clean-side” loader bucket and conveyed to the fine bark sterilised stockpile. The temperature decay in the fine bark mulch stockpile was recorded both on the surface and 400mm deep into the pile, over time.
Output was measured in continuous operation mode at 20m³ of fine grade bark mulch per hour. The material on the top and bottom steam decks flowed extremely efficiently and excellent PulseWave™ agitation was observed during the heat treatment process.
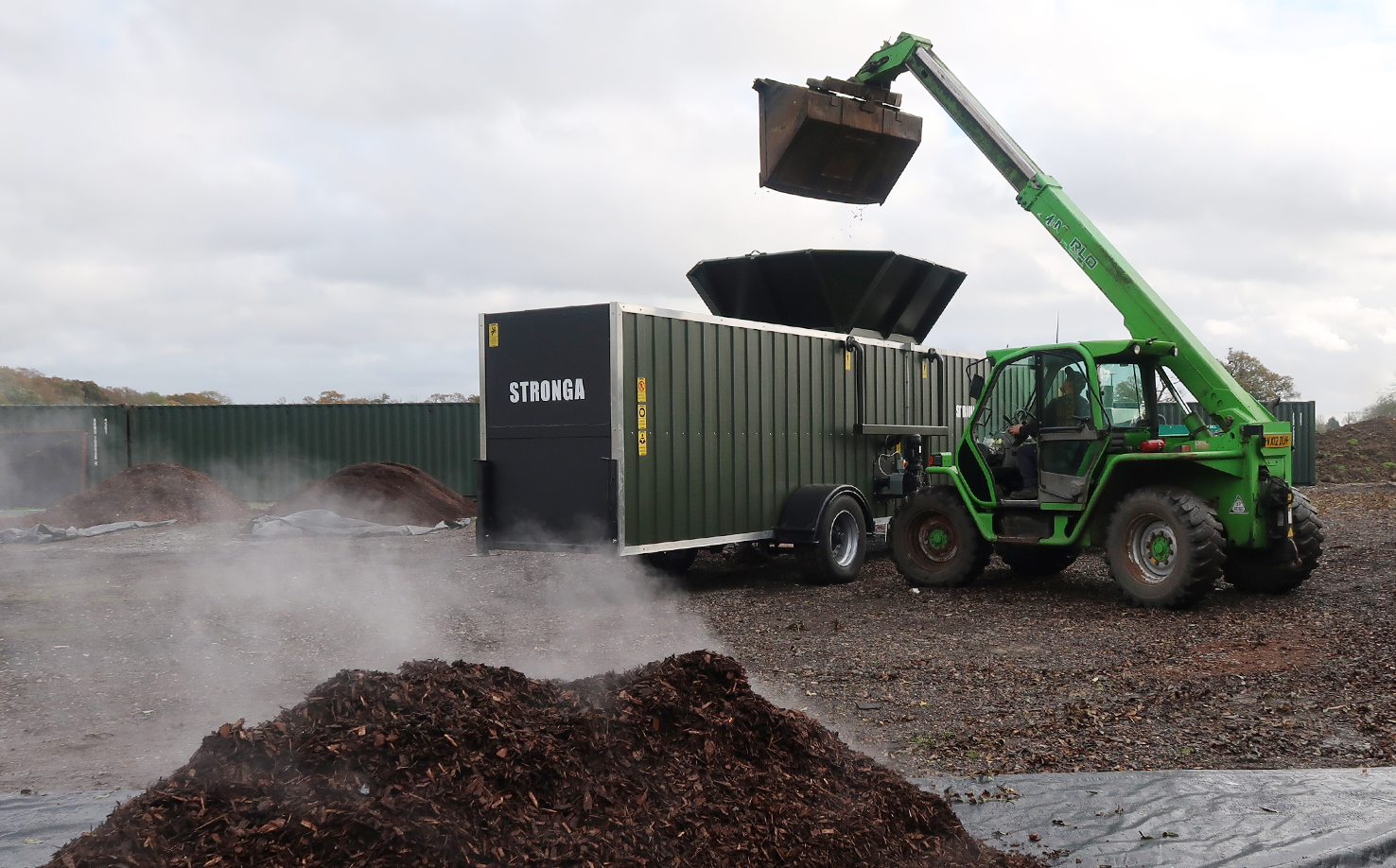
The fine bark heat treatment trial was extremely successful - far exceeding the client’s original temperature target of 56˚C for time periods inside of the in-vessel steamer exceeding the required 30 minutes. The bark material was measured to be leaving the FlowSteama consistently at 75-85˚C - a circa 60˚C temperature rise over the input material temperature. The client was particularly happy with the data logging function on the integrated HMI which allows him to evidence to local authorities the bark sanitisation process. Lab reports were able to confirm that all diseases, pests and pathogens had been eradicated from the bark mulch.
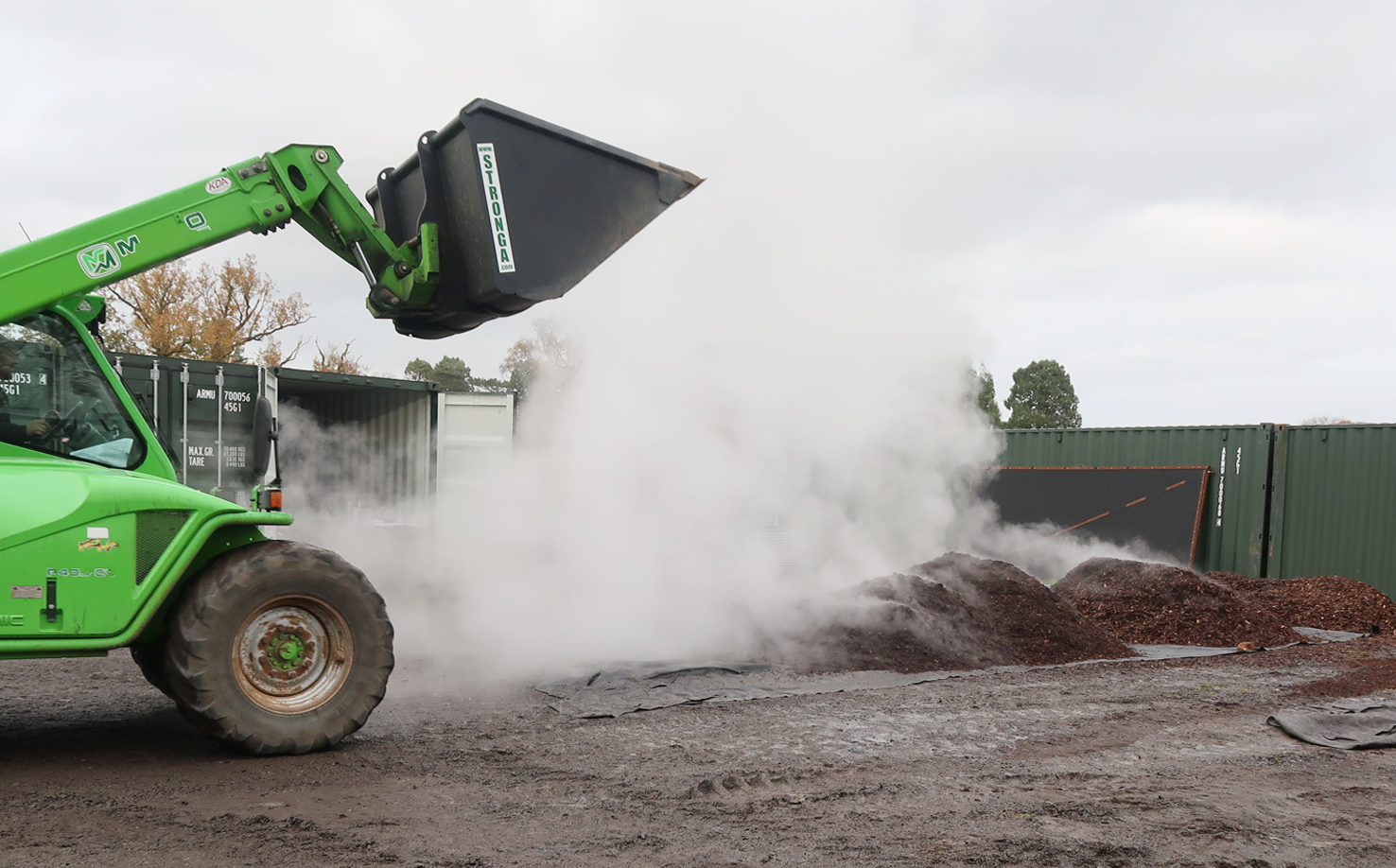
Share this post