The chart below shows carbon emissions from the concrete/cement sector in the early 2020s, compared to other industries. Whilst the percentage is relatively low at 8%, it is important to note it has increased significantly in recent decades – it was at 1% in 1950, 2% in 1990 and 4% in 2010. The trend in the cement sector is heading in the wrong direction.
Change is needed.
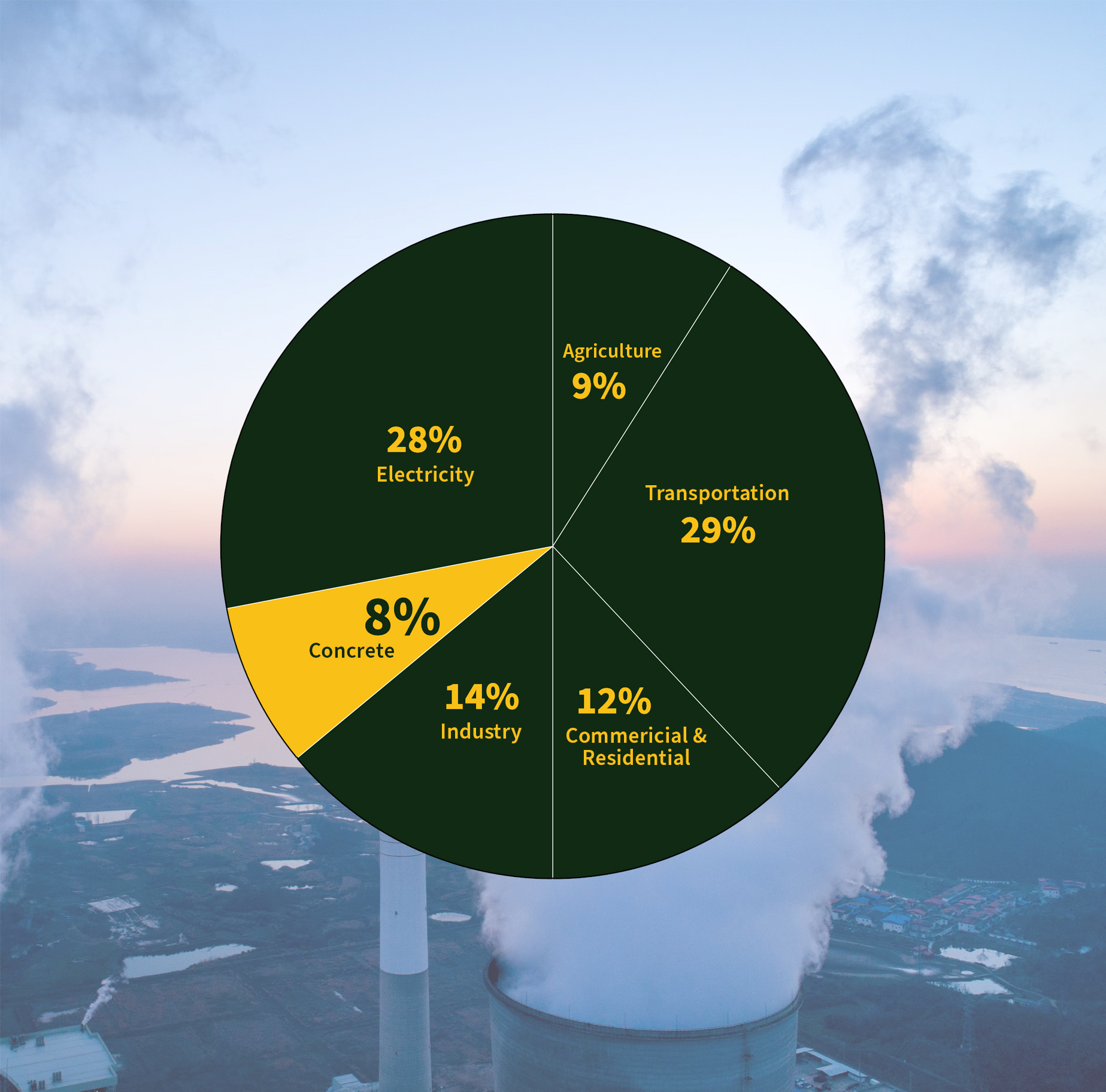
Cement - Laying the Foundations for a Carbon-Intensive Society
While cement is valued as a construction material, forming the foundation of most global infrastructure, its production process is harmful, releasing masses of carbon dioxide into the atmosphere, annually. This has huge economic and environmental implications.
Cement is made when raw materials such as limestone and clay are extracted, crushed, ground and mixed. The mix is then burnt and calcified in a high intensity rotary kiln which is powered by fossil fuels (predominately coal). This decomposed calcium oxide and carbon dioxide product is called ‘clinker’ - a key component of cement. The clinker chemical reaction process alone can account for as much as 50% of the total CO₂ emissions produced in cement production, with the remaining CO₂ emissions are from fossil fuel usage.
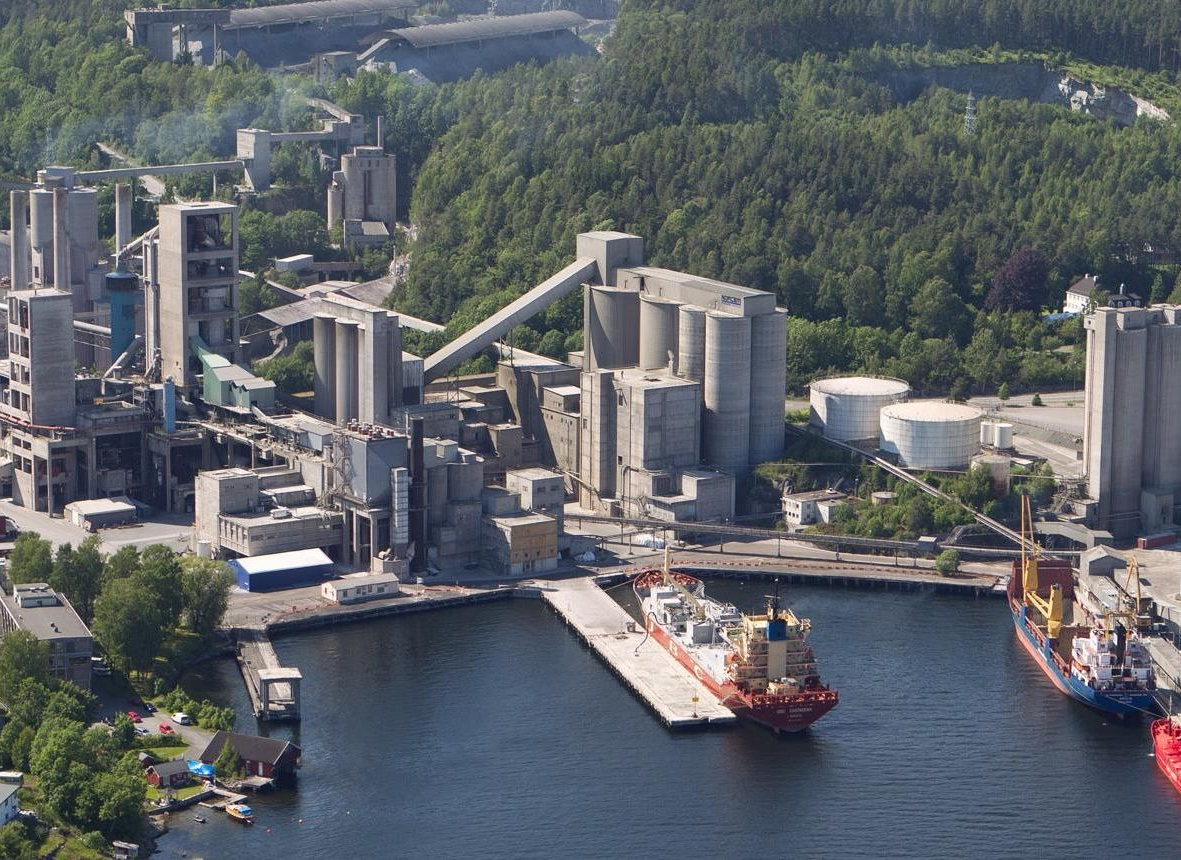
The cement industry’s total emissions (both fossil fuel energy for operations and clinker reactions) are comparable to the amount released by a large country – only China and USA emit more carbon dioxide. Records in 2022 indicate just under 2 billion metric tonnes of CO₂ had already been released from cement manufacturing alone and this will only continue to increase in the future if alternative energy strategies aren’t considered and actioned.
With many cement production companies relying heavily on fossil fuels for kiln operations, innovation is required in order for companies to meet sustainability regulations and reduce cement’s emissions per tonne, in line with ambitious 2030 & 2053 targets. Alternative forms of energy, such as SRF fluff, can contribute significantly to reducing emissions related to fossil fuel production combustion.
Coal, Oil & Gas Prices are Rising
As well as being extremely harmful to the environment, non-renewable fossil fuels are also extremely costly and increasingly taxed by governments across the globe. Realising the value and importance of cement, new programs and initiatives have been set up to help the sector migrate away from fossil fuels. Cement producers are being urged to adopt alternative ‘non-fossil fuel’ powered production methods to minimise environmental degradation and economic costs.
With rising costs harming their bottom-line, a Turkish cement production company recently approached Stronga with the aim of drying SRF fluff to optimise their alternate energy usage, thus decarbonising their cement production site.
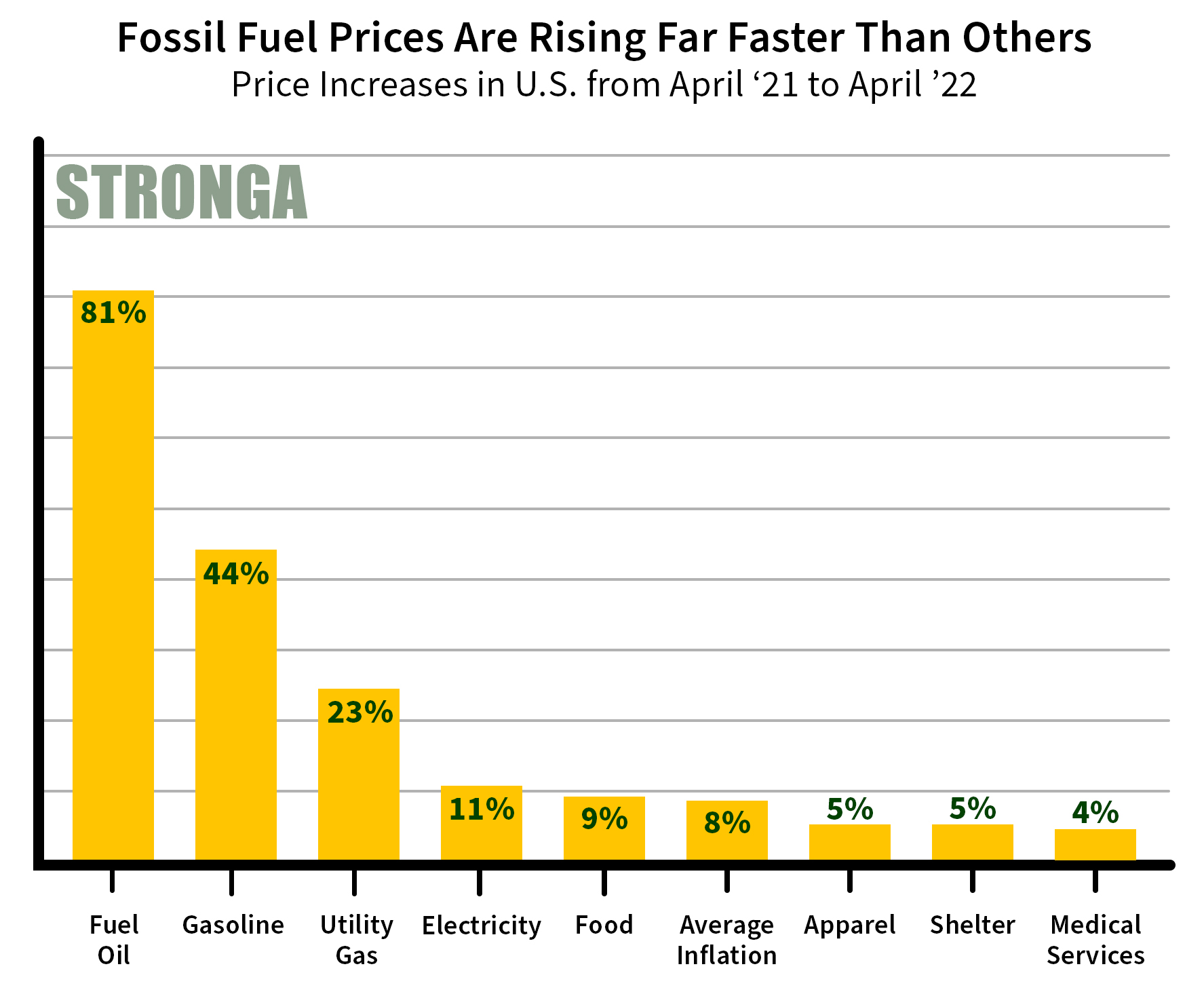
Waste 2 Energy
Alternative fuels are derived from non-fossil fuel sources, examples of which include tyre crumb, waste/landfill biomass and SRF pellets. By using waste produced from other sectors as alternative energy for their own production, our client in Turkey has made significant reductions to their carbon tax and greenhouse gas emissions. Using non-recyclable waste, destined for landfill, as fuel to power kilns for cement production, allows ‘greener’, less pollutive energy to be utilised at a significantly lower cost.
SRF (Solid Recovered Fuel) has the potential to yield high calorific energy which is an essential requirement for cement plants, however its moisture content can vary across seasons and grades which can cause issues for the cement production process. It is important that SRF fluff is conditioned and dried before use in the kiln; otherwise, the fuel will be considered out of profile and unsuitable.
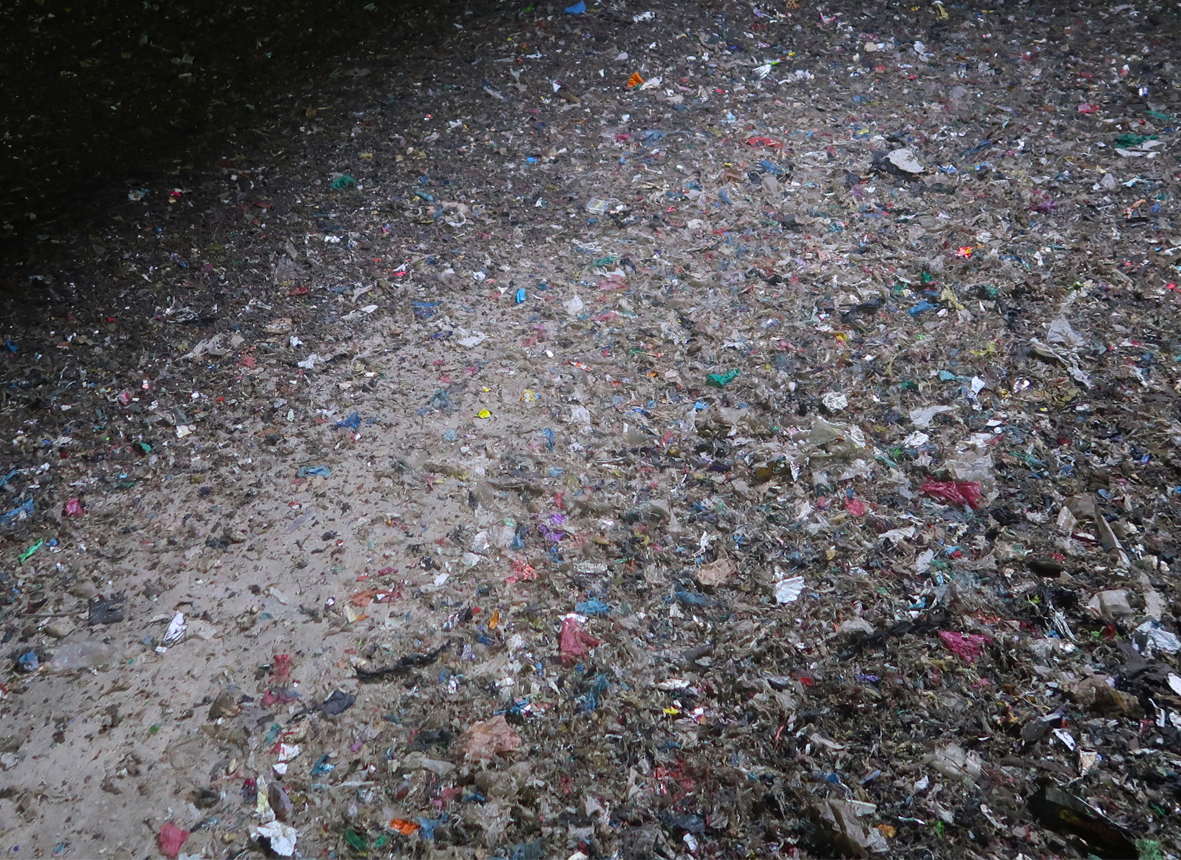
A cheaper and more sustainable alternative to fossil fuels, SRF has the potential to be transformative in the cement industry, lowering fuel costs, reducing fossil fuel emissions, minimising landfill waste and reducing the cement industry’s coal dependency. Stronga’s FlowDrya SRF dryer utilises this client’s abundant supply of residual thermal energy from their on-site kiln, enhancing energy conservation of the operation.
Our client, who recently became the first Turkish cement company to commit to net zero, wanted to reduce their GHG emissions by over 20% by the year 2030. Stronga played a small but vital role in ensuring the SRF was conditioned to the optimal moisture content to maximise tonnage throughput, while adding significant caloric value to the material. The chart below indicates the importance of migrating from fossil fuels to SRF (alternative energy).
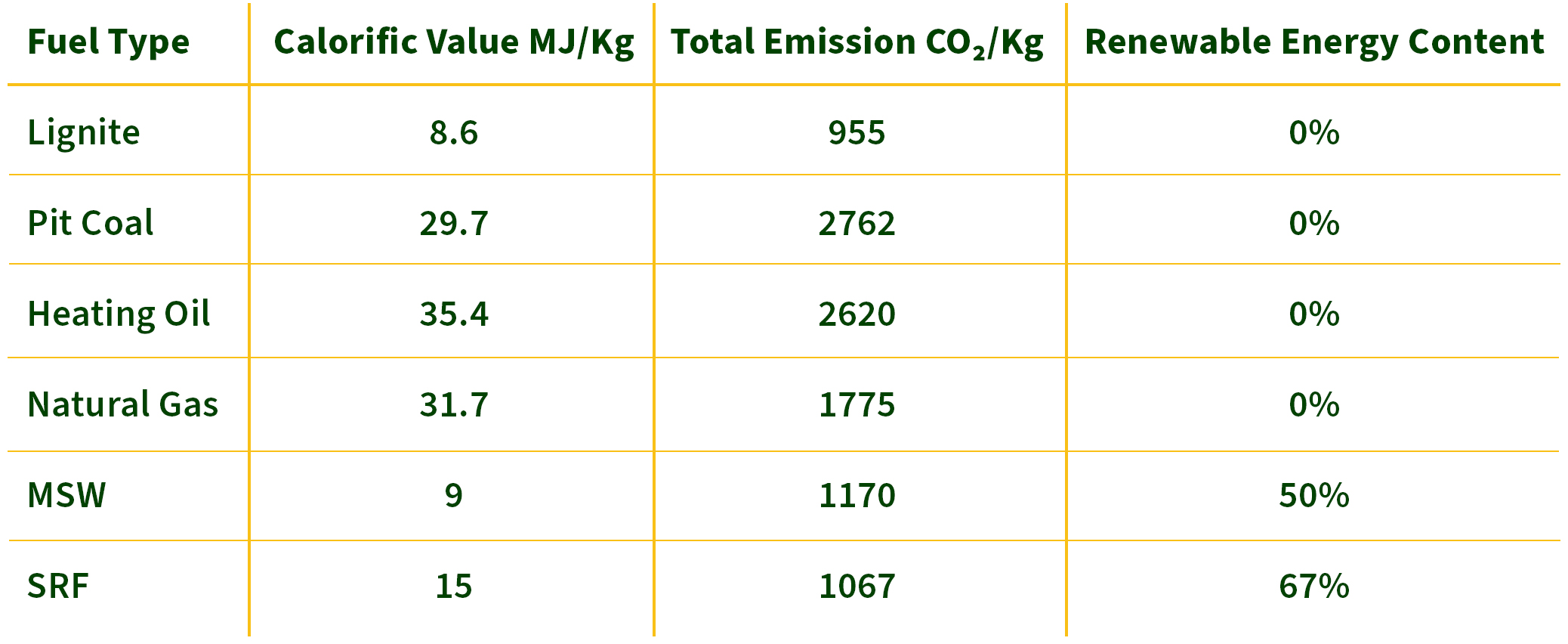
The Perks of Localised Alternative Energy
Utilising local SRF together with residual thermal energy from the plant’s onsite rotary cement kiln allowed our client to become entirely energy-independent, operationally-resilient and even more competitive in the cement market. Overall, long-term financial savings and lower carbon footprints are anticipated. Discover the other key benefits of producing on-site alternate energy:
✓ Independence from the fossil fuel market, meaning external factors which cause fossil fuel prices to rise do not directly affect cement production costs.
✓ Cement production plants using alternative fuels together with residual kiln energy will be viewed more positively in light of virtuous circular economies.
✓ As long as there is a waste supply, SRF can be converted into energy and used for cement operations and kilns.
✓ Reduced operational costs and less carbon taxed.
✓ Increased flexibility over energy choices.
✓ Reduced waste to landfill.
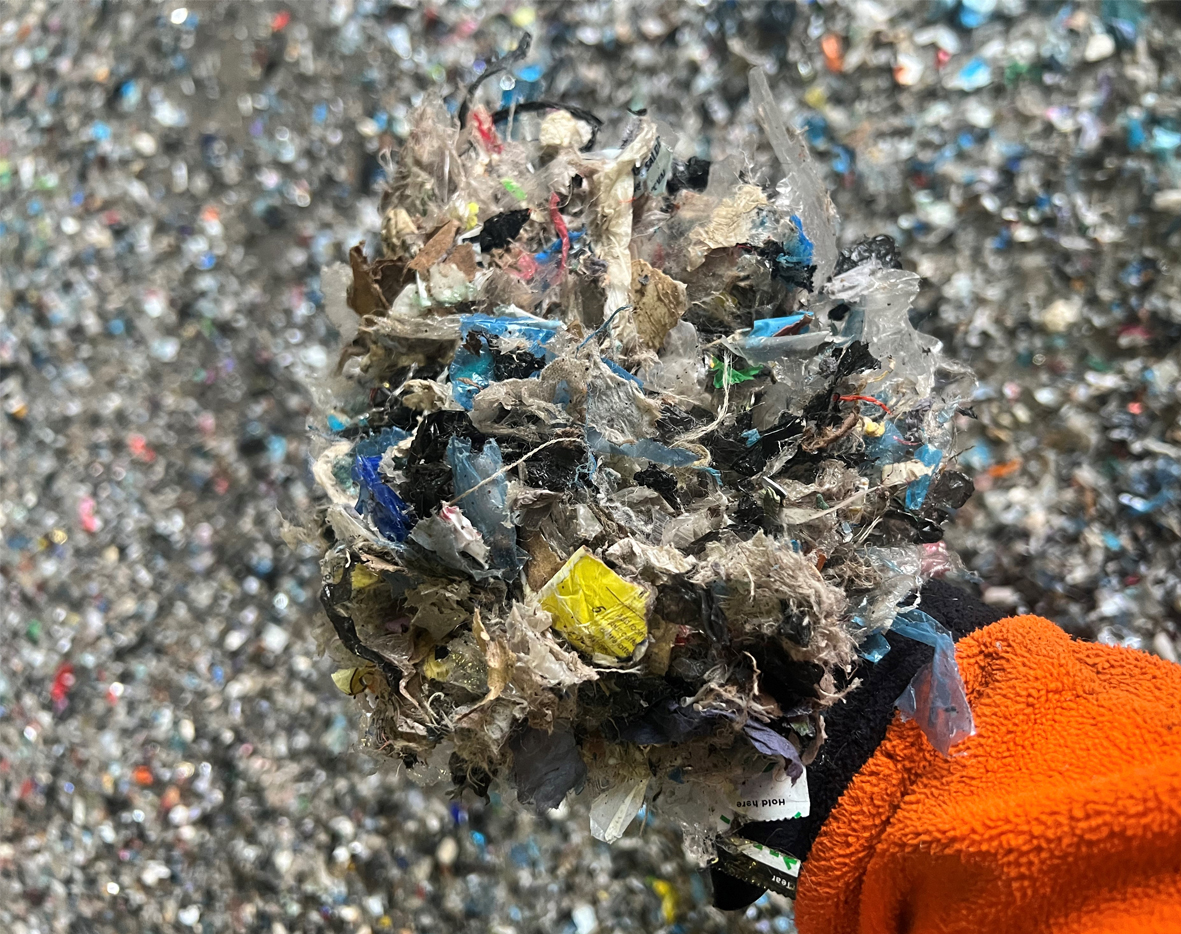
Optimising Cement Production Through Drying SRF Fluff
SRF often arrives on cement sites out of moisture profile, especially during wetter seasons. In order to be considered usable and sustainable, SRF moisture content should be reduced to at least 20% before being loaded into the kiln. If the fuel isn’t adequately dried, it can cause operational complications whilst also releasing moisture related emissions (VOCs). Drying SRF significantly increases the calorific value of the material whilst reducing cement production CO₂ emissions from fossil fuels.
Dried SRF is not only more stable and easier to process, it also allows as much as double the amount of energy to be fed into the kiln, allowing for consistent cement production at a lower cost. As the FlowDrya has already removed the moisture from the SRF, no additional energy is required to do this in the kiln, thus the dryer facilitates increasingly efficient production values.
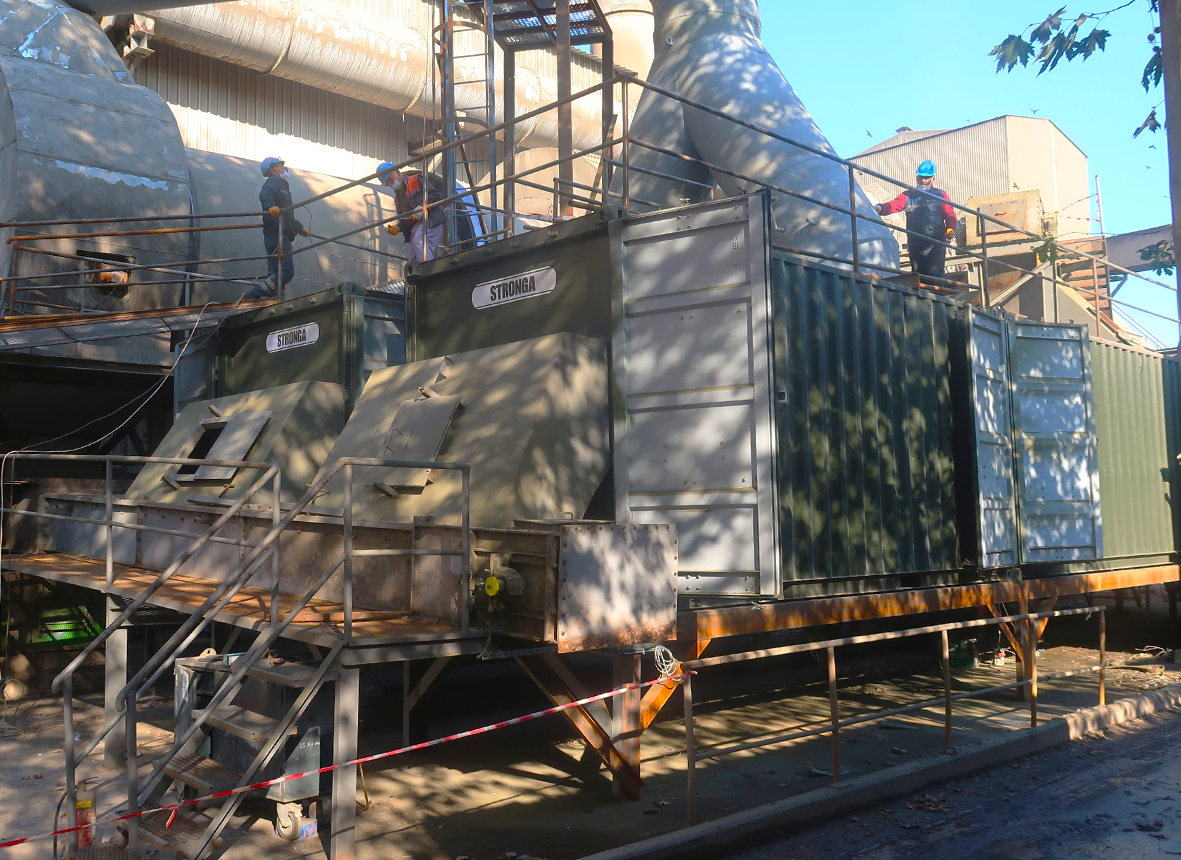
SRF Utilisation; Year-Round
As the chart below shows, our client has an ongoing annual battle against high precipitation in the months of December, January, April and May. Investing in FlowDrya SRF drying equipment, means climate no longer hinders the client’s abilty to use SRF which often arrives sodden during this time. FlowDrya allows them to utilise dry SRF all year-round, providing them with suitable alternative energy for kiln heating and cement production.
Please note - funding may be available to those companies actively reducing CO₂ emissions through ‘cleaner’, alternative fuel practises. Stronga suggest customers research the various schemes available in your region to discover any funding opportunities.
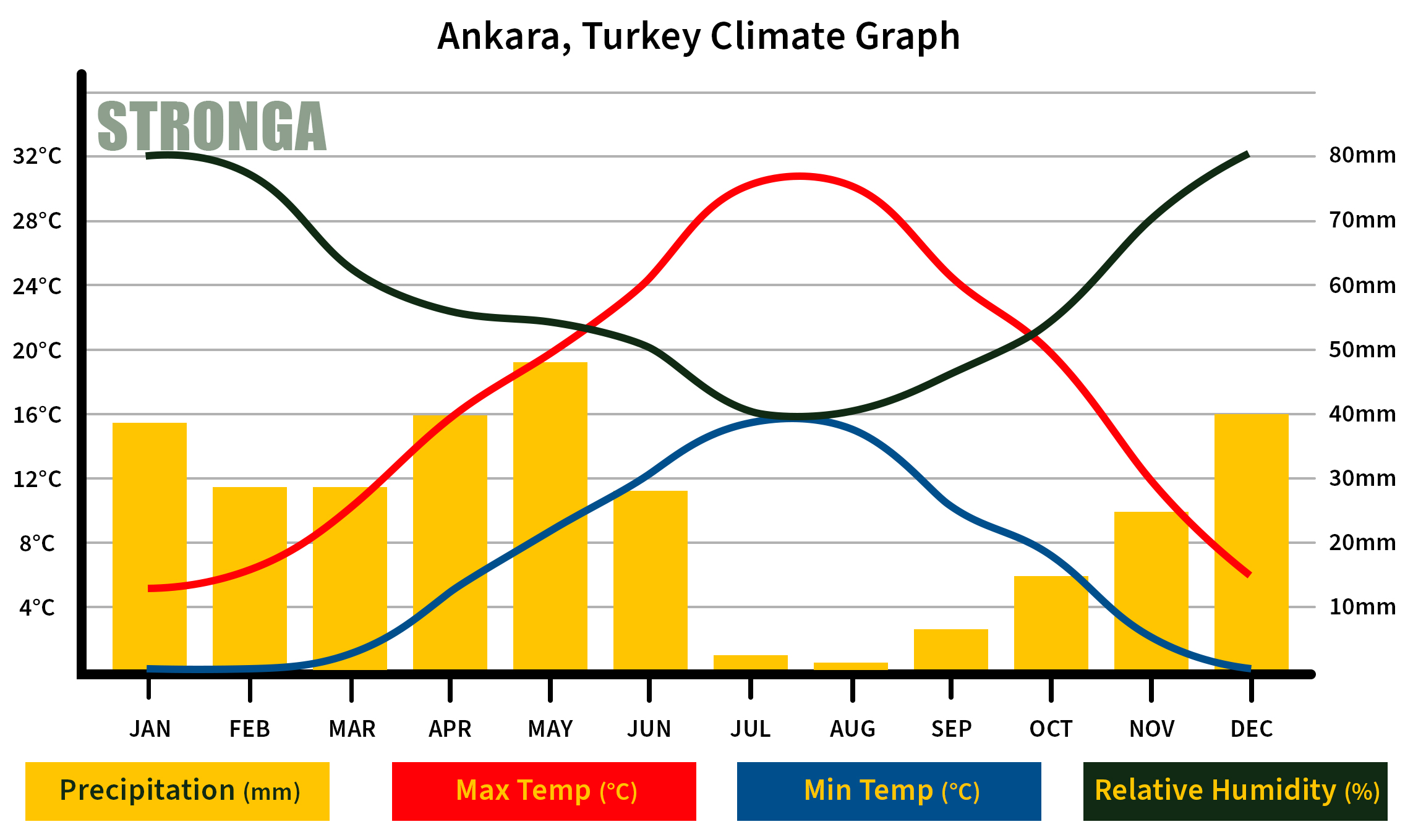
Why is FlowDrya Suited to SRF Drying on Cement Plants?
Our client took the progressive leap towards using alternative fuels to improve the operations of their well-established cement production plant. This tough decision was relieved through collaboration with Stronga’s engineers who advised on the project and designed two bespoke “FD38” International-Series dryers to deliver the necessary SRF criterion.
FlowDrya equipment is particularly well suited to SRF material because each dryer is individually crafted on a project-by-project basis to suit the individual properties of the material, local climate and more. To suit this particular cement production process, we designed two modular dryers which were specifically-suited to the SRF specification and local climate in Ankara, Turkey. The two highly automated SRF dryers accept and convey wet and dry SRF material, as well as available low humidity residual kiln heat, reducing labour operation costs.

Stronga SRF Drying Equipment is…
- Simple and uncomplicated with no belts and very few bearings, significantly reducing fire risk and maintenance costs.
- Equipped with a fines auger which filters the material, ensuring no ‘non-SRF’ materials are used in the kiln.
- Hydraulically powered with PulseWave™ agitation system ensuring consistently dried, highly calorific output.
- Environmentally-friendly; accepting residual heat while diverting SRF from landfill.
- Highly reliable with continuous duty operation cycles up to 8,500 hours per annum.
- Fitted with DryStation™ HMI controls which log and monitor moisture parameters.
- Small and compact and can be scaled according to the customer’s requirements.
- Easy to integrate together with existing on-site equipment (conveyors & more).
- Available with anti-corrosion stainless steel for certain corrosive materials.
- Equipped with airflow zoning to ensure effective moisture removal.
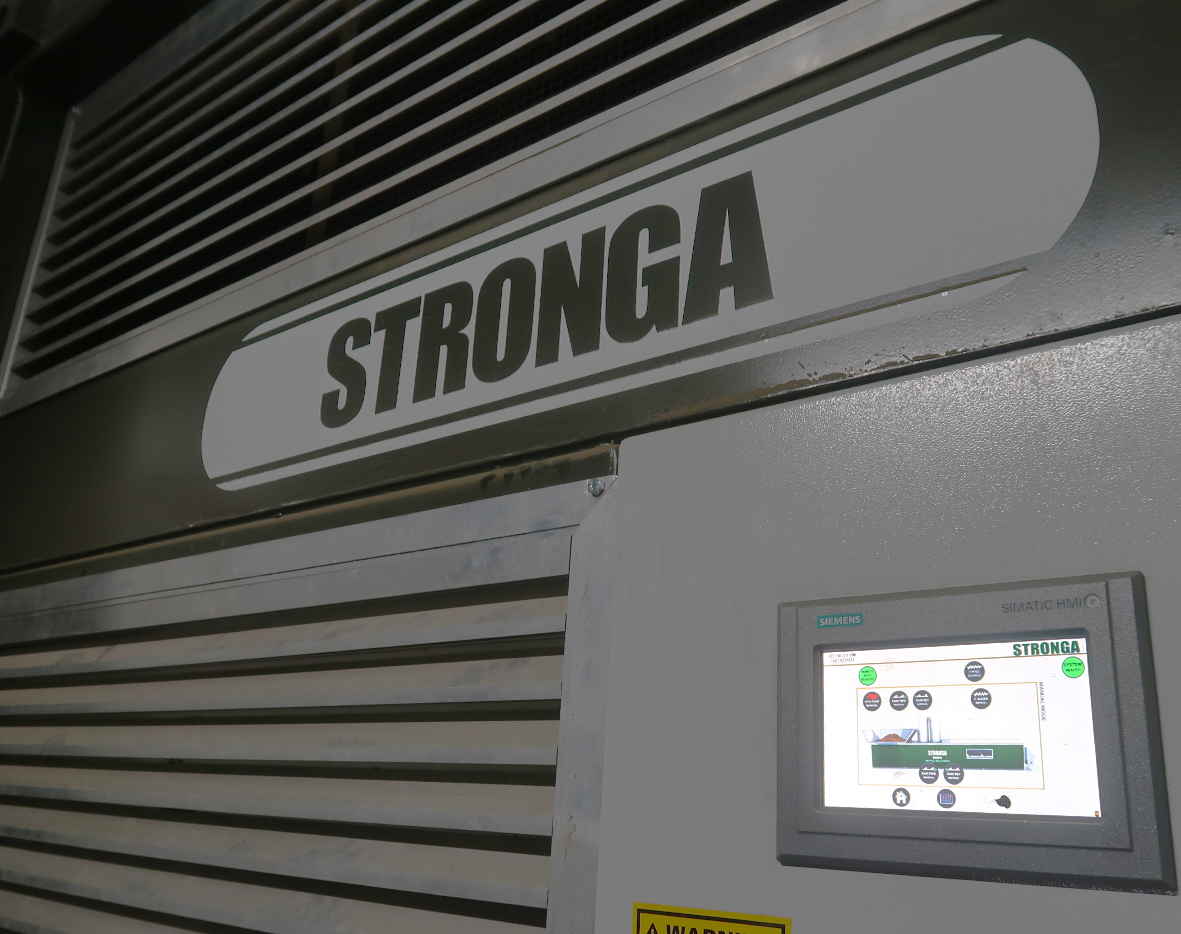
Decarbonise for a Better Future
By recovering the material value of waste (SRF) through drying, extortionate long-term cost savings and atmospheric GHG reductions can be made. Recognised for their postive achievements and contribution to alterantive energy usage in the cement industry, our client’s operations have now become even more efficient through making the smart investment in FlowDrya SRF drying systems.
Enquire today to discuss your project with the Stronga team. Open your eyes to a wealth of experience and alternative energy opportunities – info@stronga.co.uk
Share this post