Solid Recovered Fuel (SRF) is a refined, high-calorific fuel made from non-hazardous waste, and it offers a promising solution in enabling cement plants to reduce their reliance on expensive fossil fuels while lowering carbon taxes (see illustration of carbon taxes across Europe below).
Energy intensive industries, such as cement production, have created a growing demand for dry, low moisture SRF, providing opportunities for businesses in the waste recycling sector to increase their profits. This not only allows the recycling sector to divert waste from landfill, thus avoiding increasingly expensive landfill costs and taxes, but also creates a potential income stream through the sale of consistently-dry, conditioned SRF. This preserves increasingly scarce, non-renewable natural resources.
Learn more below.
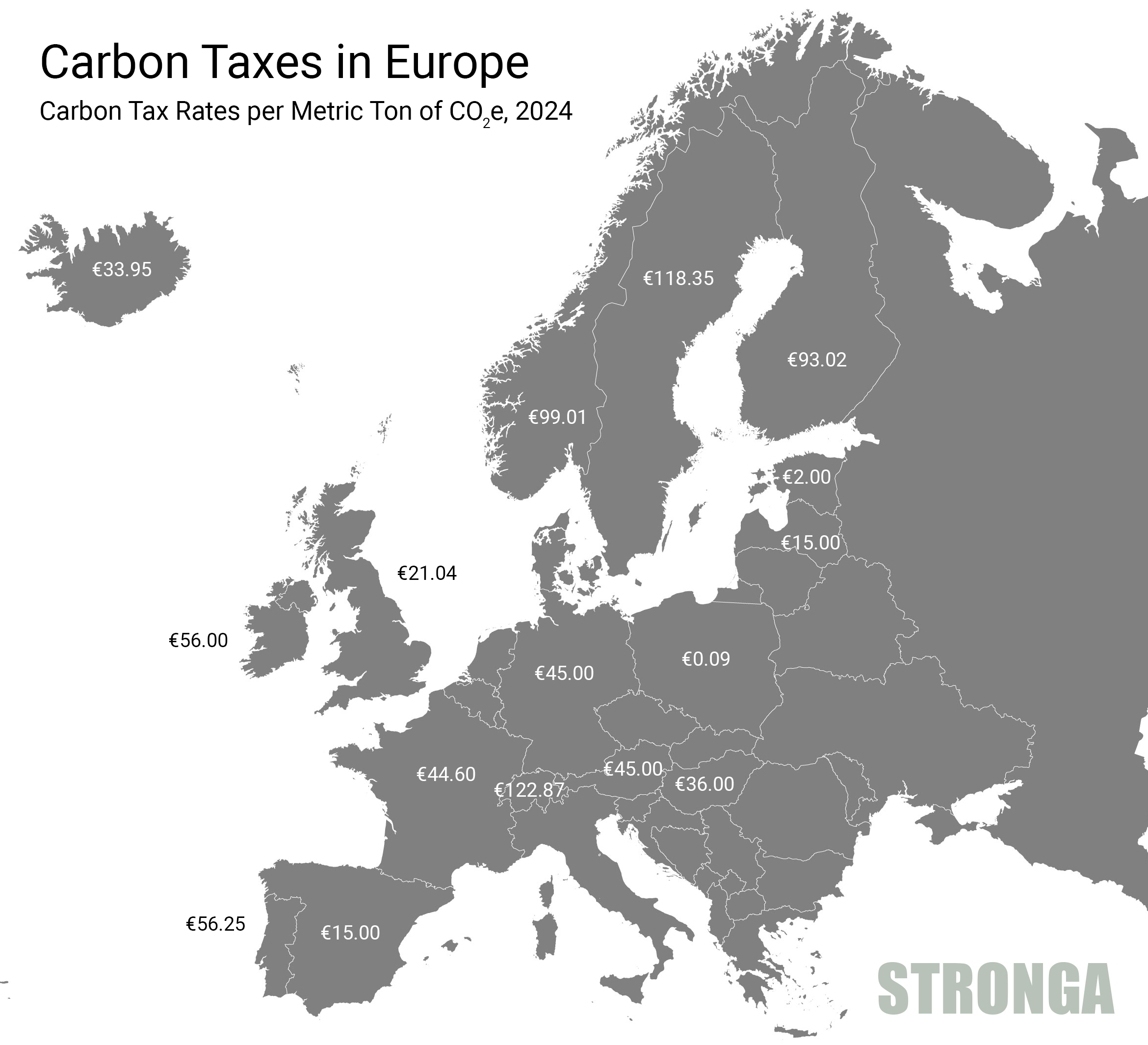
The Role of SRF in Cement Production
The process of cement production involves heating raw materials to extremely high temperatures in rotary kilns, where the formation of clinker, the main component of cement, occurs. Traditionally, fossil fuels like coal have been the primary energy source for this process. However, SRF offers an alternative solution, derived from municipal solid waste and industrial residues, which can be combusted to supply the thermal energy required.
Using SRF delivers circular economy benefits, diverting waste from landfills while recovering highly useful energy. Successful combustion of SRF demands that moisture content is consistent and below 20% with cement plants imposing financial penalties for material that arrives out of profile (moisture content above 20%). Stronga offers an effective solution for drying SRF in the form of the FlowDrya where consistent and reliable drying ensures penalties do not incur, and, below 20%, there is actually real profit potential.
Note – Figures have been omitted from the graph below because they vary on an individual market/cement plant basis. Whilst cost penalties can be substantial at certain high moisture contents, there is a positive situation for sub-20% moisture SRF where businesses can actually be paid for the material. Potential buyers including cement and lime producers, waste to energy plants and large industrial heat users such as brickworks, paper mills and so on.
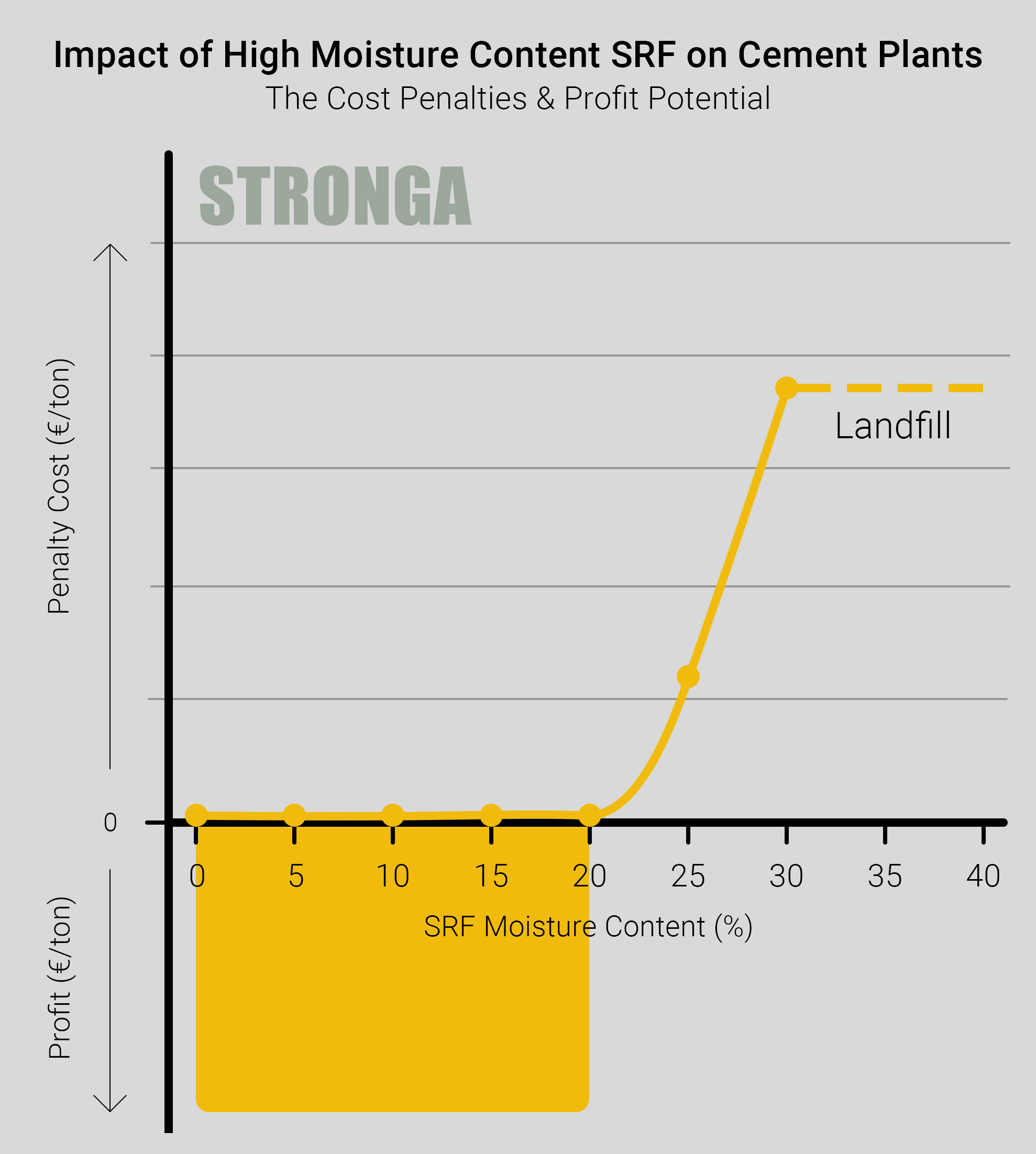
Why Moisture Matters: The Problem with Wet SRF
SRF with high moisture content poses significant challenges and inefficiencies in cement kiln operations and waste to energy plants, exacerbated by seasonality and climatic conditions, where the moisture content of SRF increases during wet weather.
The key issue lies in the calorific value (the amount of energy released during combustion). Moisture in the SRF absorbs heat during evaporation, which reduces the net energy available for the kiln process; this causes thermal inefficiencies. Stronga’s SRF conditioning and drying solutions provide consistent moisture characteristics of SRF, reducing the moisture content down to below 20%.
Learn more about FlowDrya International Series for drying SRF >
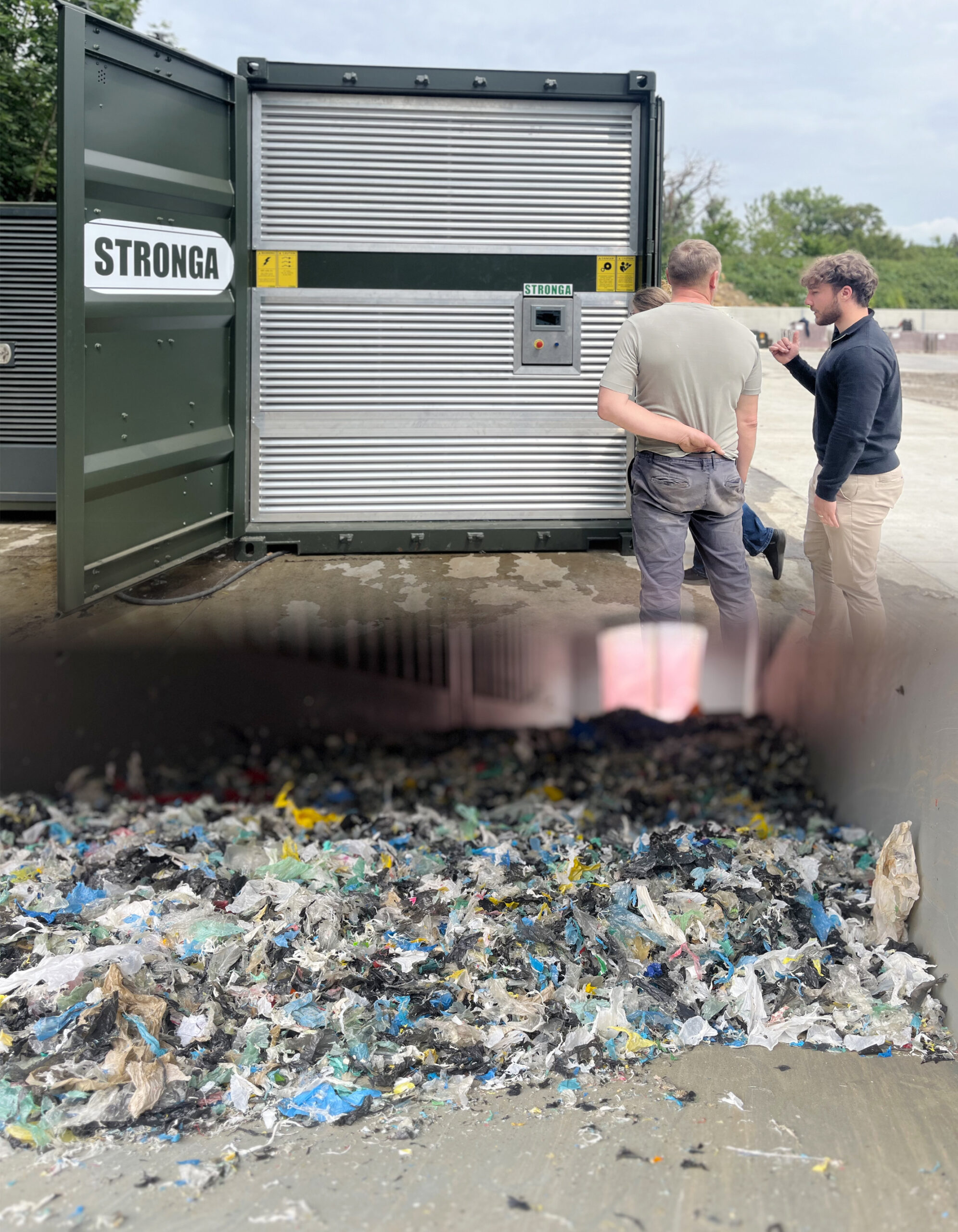
Discover what happens when wet SRF is fed into cement kilns.
• Lower Energy Value: As moisture content of SRF increases, more of the kiln’s heat energy is diverted to evaporate water in the SRF, rather than to raise the temperature necessary for clinker formation. This decreases cement production and kiln output capacity, as the limits of the feed system are reached. Higher moisture contents of SRF, over 20%, also leads to extensive waste heat loss (steam) via the flue.
• Flame Instability: Kilns require a stable, high-temperature flame to maintain process consistency. Inconsistent moisture fuel leads to incomplete combustion and fluctuating temperatures. This leads to poor heat distribution in the burning zone.
• Operational Instability Risks: Excess moisture can lead to higher emissions of unburned hydrocarbons, higher particulate matter release, VOCs and physical damage to kiln components due to thermal stresses.
• Increased Fuel Consumption: To compensate for the lost energy in evaporating moisture, more fuel must be burnt, negating the economic and environmental benefits of using SRF as an alternative fuel.
Compounding all of the above together, the operational difference between a conditioned stable <20% SRF and a higher, variable moisture content SRF is beyond compare.
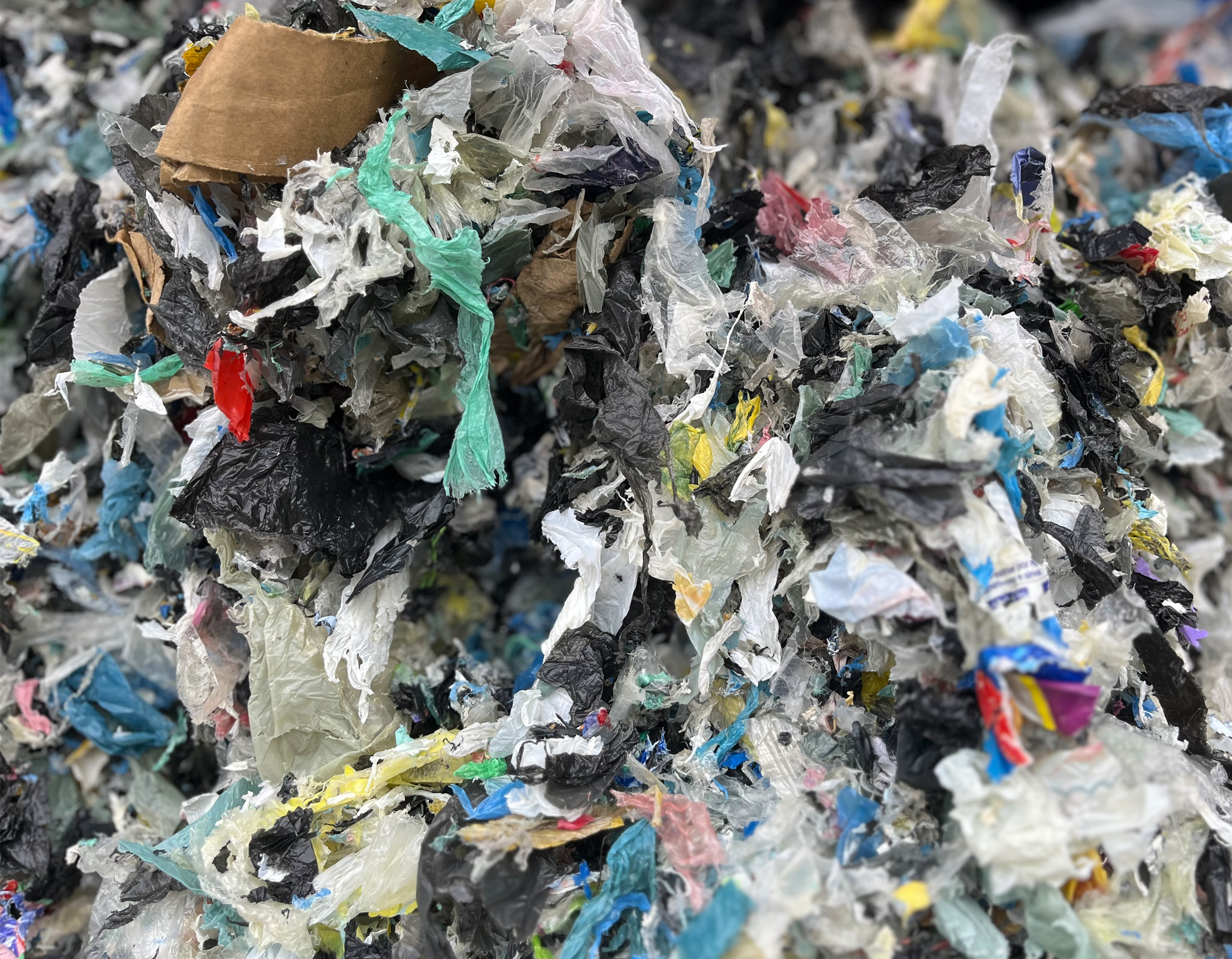
FlowDrya Increases the Calorific Value of SRF
According to recent studies on fuel characteristics and combustion behaviour, drying SRF significantly improves its performance in cement kilns. Optimal SRF typically contains less than 20% moisture content, ensuring high energy density and predictable combustion behaviour. FlowDrya reduces the moisture content of wet SRF from as much as 40%, or higher, down to below 20%, consistently across the load.
The graph below shows that drying delivers significantly more useable energy per kilogram of fuel. FlowDrya, by delivering a consistent below 20% moisture content, significantly improves fuel stability, reduces variability, and helps meet stringent stack emission standards.
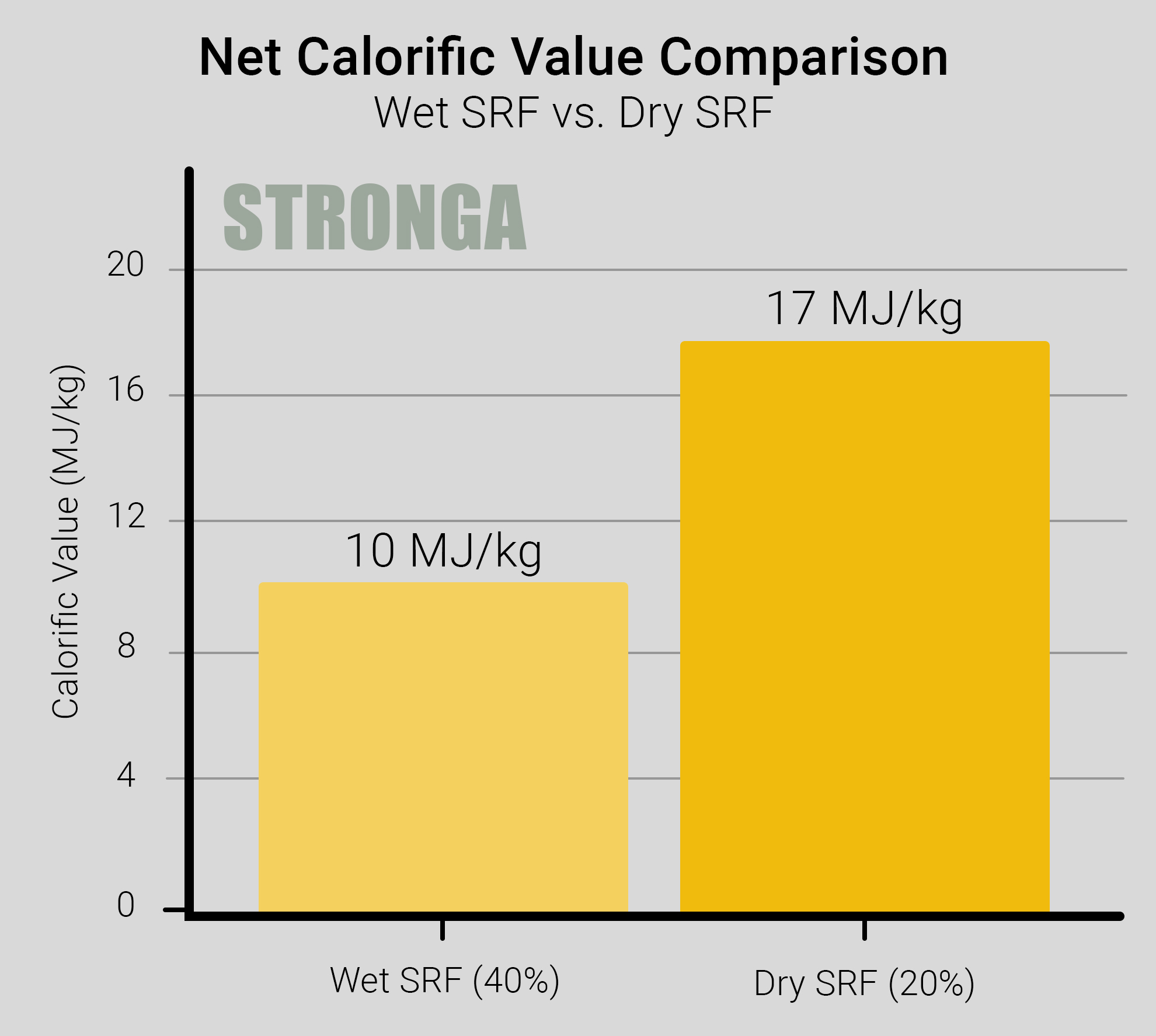
Drying Efficiency Using Residual Heat
Cement producers have access to considerable levels of residual heat which can be used for the SRF drying process. For every 4GJ of thermal energy required for a tonne of cement produced, as much as 50% of this energy is lost as waste heat. FlowDrya utilises residual heat from cement production to dry SRF, creating a circular, on-site process. As a by-product of cement production, this heat has a nominal cost – making the investment in FlowDrya equipment even more attractive.
The last 5 years, in particular, have seen high inflation in energy costs. Directing available residual heat to the FlowDrya for the SRF drying process helps combat this rise in energy cost by taking control of the raw material, replacing increasingly expensive gas with cheaper, readily available SRF.
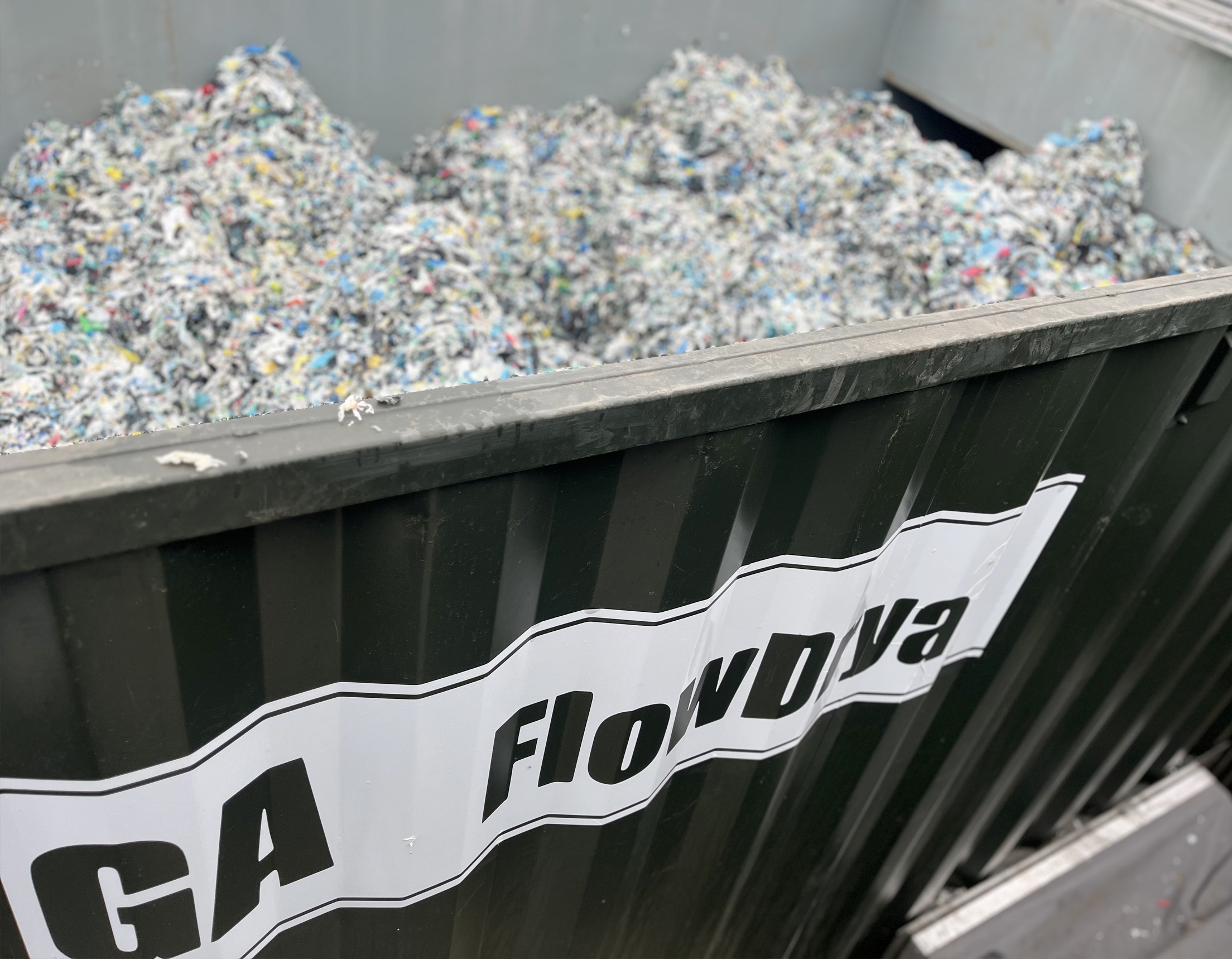
SRF Drying Video
FlowDrya’s deep-drying-bed process with PulseWave™ agitation delivers high throughput of a consistently dry SRF material. Watch FlowDrya in action, drying SRF, in the video below.
SRF Quality is Dependent on Moisture Content
Wet SRF is unsuitable for direct use in cement kilns; it reduces fuel efficiency, destabilises combustion and increases emissions. FlowDrya forms part of the integral conditioning process where wet SRF becomes a viable alternative fuel, in cement manufacturing.
Maximise the financial and environmental benefits of alternative fuels; get in touch with Stronga today to tailor your FlowDrya to your individual SRF drying requirements. Don’t waste a good opportunity, contact enquiries@stronga.com
Please note - cement kilns that use alternative substitute fuels derived from waste as part of co-processing, must comply with local legislation and requirements. In the UK, this falls under the Industrial Emissions Directive. More information is available here >
Share this post