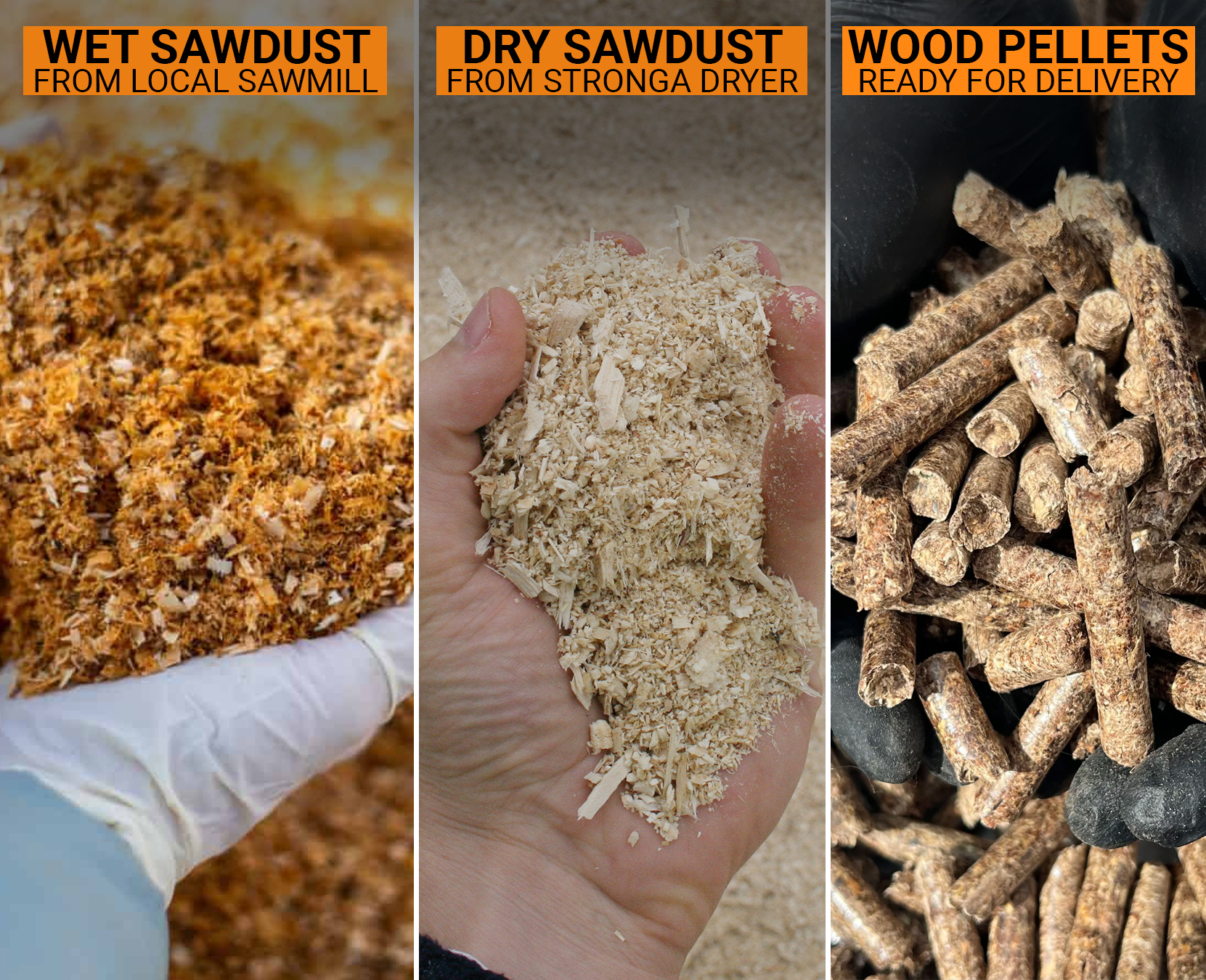
Global Climate Warning
Research shows that since the industrial revolution, the amount of CO₂ in the atmosphere has increased by approximately 50%. Not only are fossil fuels an increasingly expensive source of energy, they also have geopolitical implications. If alternative options aren’t explored, continued warming will lead to increased droughts, wildfires and sea-level rises, as well as disruptions to coral reefs, plants and animals. Businesses are increasingly attempting to avoid using expensive fossil fuels to reduce the destructive effects of heat-trapping CO₂.
Providing it has been sustainably sourced, biomass-based pellet fuel has been highlighted as one solution to mitigate the harmful effects of fossil fuels and contribute to a sustainable future. The management and sourcing process must be monitored for wood pellets to be considered truly cleaner and greener.
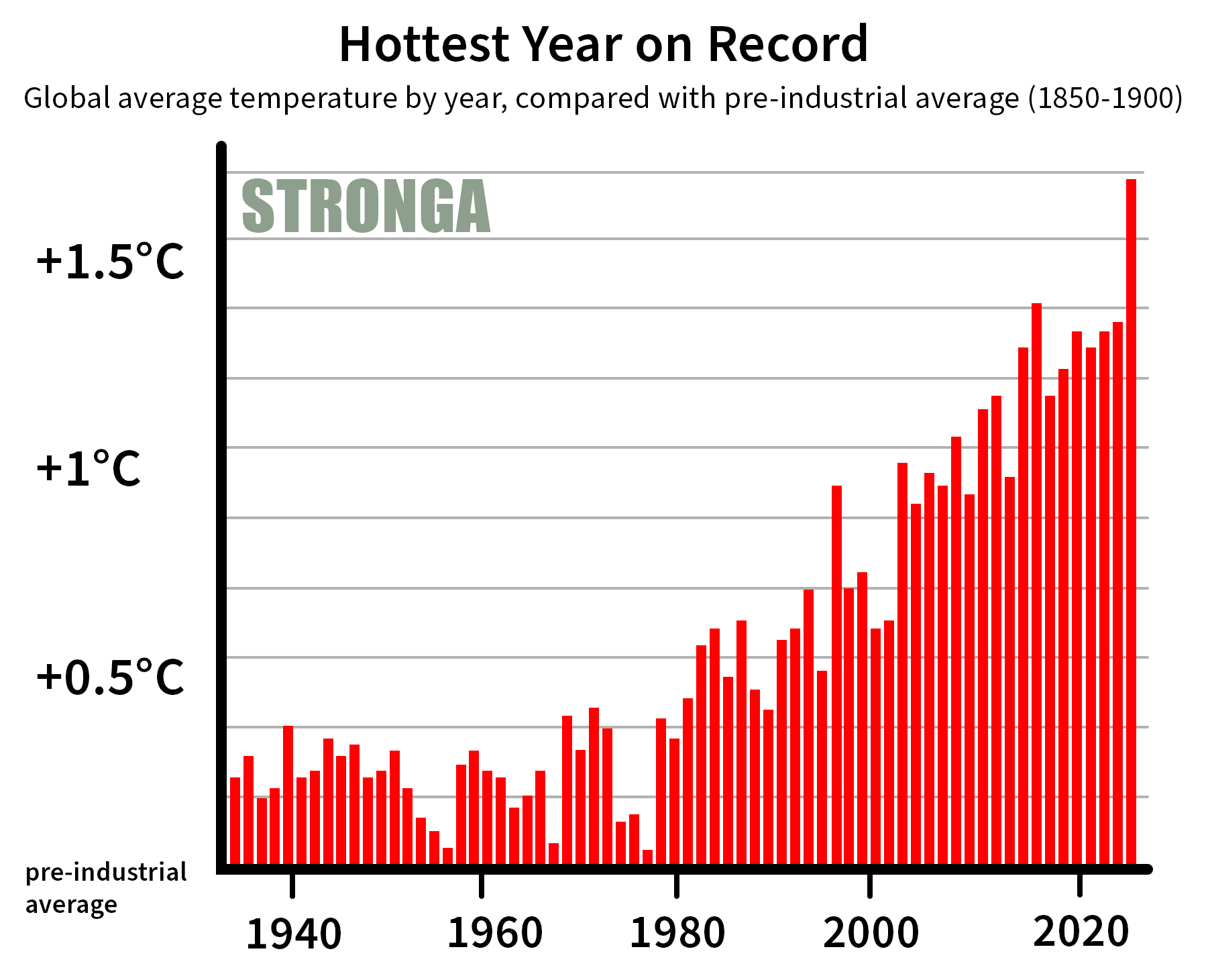
Pellet Power – The Biomass Market
Woody biomass is a regionally available resource which has proven more stable when compared to other fuels like coal which have increased in price significantly of late. Wood pellets have been seen as an attractive alternative to fossil fuels and as a result, manufacturers are often unable to fulfil demand, particularly during winter months.
Wood pellets can be used for cogeneration, CHP, power generation and domestic energy requirements, providing a less toxic, more renewable supply of alternative energy. They can be produced on bulk, easily stored and transported effortlessly, while biomass CHP will often qualify for heat and electricity subsidies.
Forecast demands for pellet fuel indicate a continued increase over the coming years. Estimates indicate the global demand for industrial wood pellets is set to reach 36 million tonnes by 2027, meaning that demand would have increased by over 50% since 2017. The graph below confirms this projection and highlights the increased demand across 7 countries from 2016-2024. Demand in the UK, France and other EU countries has again, almost doubled.
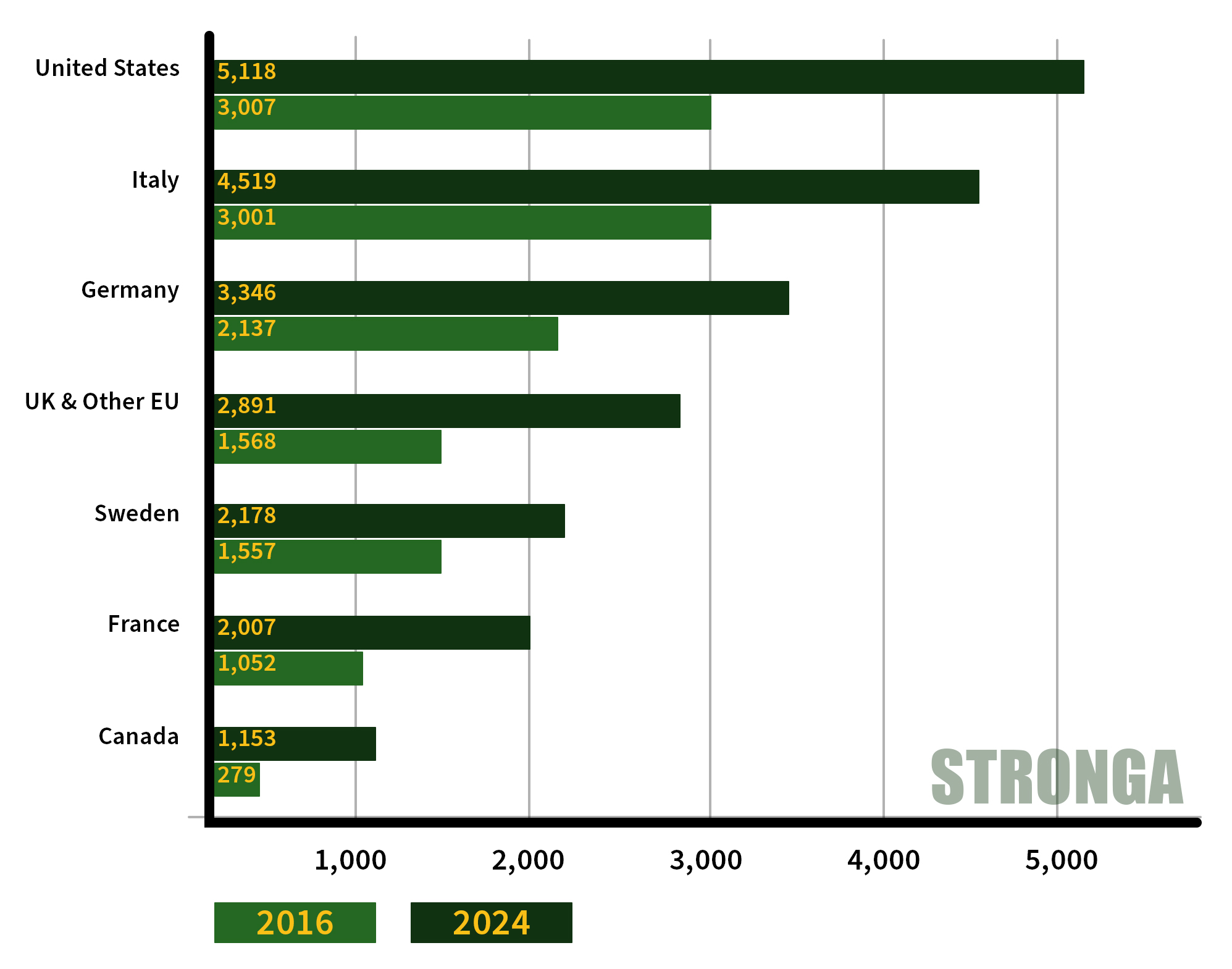
Forestry owners and sawmills are among those businesses that have already sensed an opportunity to use mill residues to produce and sell wood fuel pellets, while demand is increasing. However, in order to ‘greenify’ the economy while remaining competitive in the pellet industry, increasing sustainability regulations need to be carefully considered.
Are Wood Pellets Considered a Sustainable Alternative Fuel?
Australia has set a precedent by becoming the first country to review its sustainability classification of woody biomass pellet fuel. Despite the generally positive publicity surrounding wood pellets, Australia legislation now focuses on the sourcing of wood, discouraging felling and habitat destruction. If, for example, biomass is sourced by chopping down native trees, pelleting cannot be considered a sustainable and renewable alternative to fossil fuels.
New regulations also focus on the emissions released from burning wood pellets and the renewable aspect of wood fuel. Although woody biomass can be considered a renewable energy source, it has lower combustion efficiency than coal and the renewability aspect is slow. Re-planted trees will, however, eventually grow so pellets are therefore more sustainable than fossil fuels.
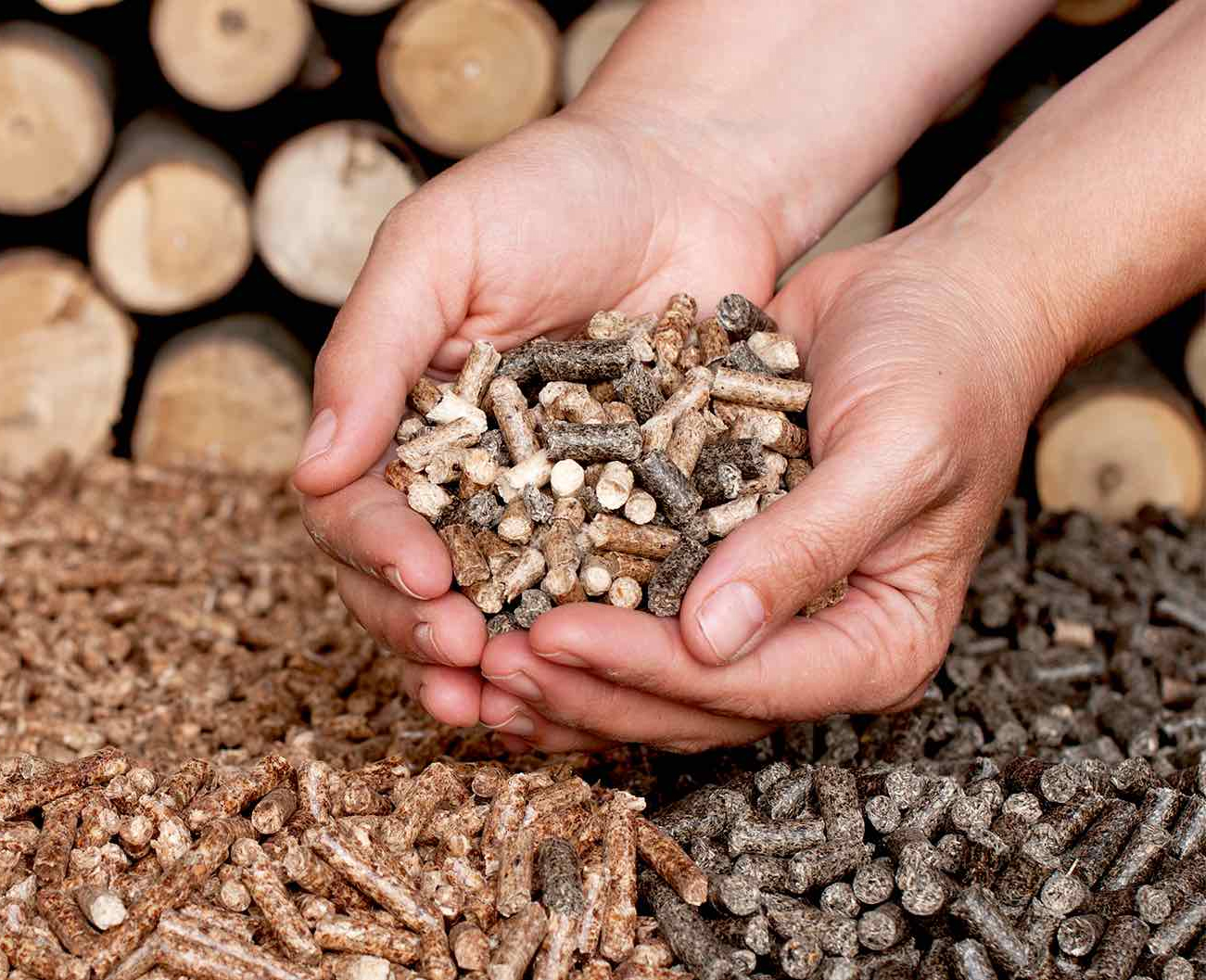
Stronga Collaborates with a Sustainable Wood Pelleting Company
Stronga have recently been involved in discussions with an eco-conscious pelleting company in Tasmania who have managed to incorporate the positives of pelleting using woody biomass whilst addressing the negative connotations. They have succeeded in producing CO₂-neutral pellets from residual sawmill material (sawdust) that has been internationally-approved as environmentally-sustainable - thus abiding to new legislation in the region.
Stronga believe they have adopted a fair approach to sustainable pelleting through producing low moisture, non-acidic wood pellets with high combustion efficiency and no chemical binders, striking a balance between high energy demands and reduced reliance on fossil fuel usage. By focusing their biomass sourcing on residual and dead wood for pellet production, their sustainability prospect aligned with Stronga’s philosophy of transforming waste residue to high value resource.
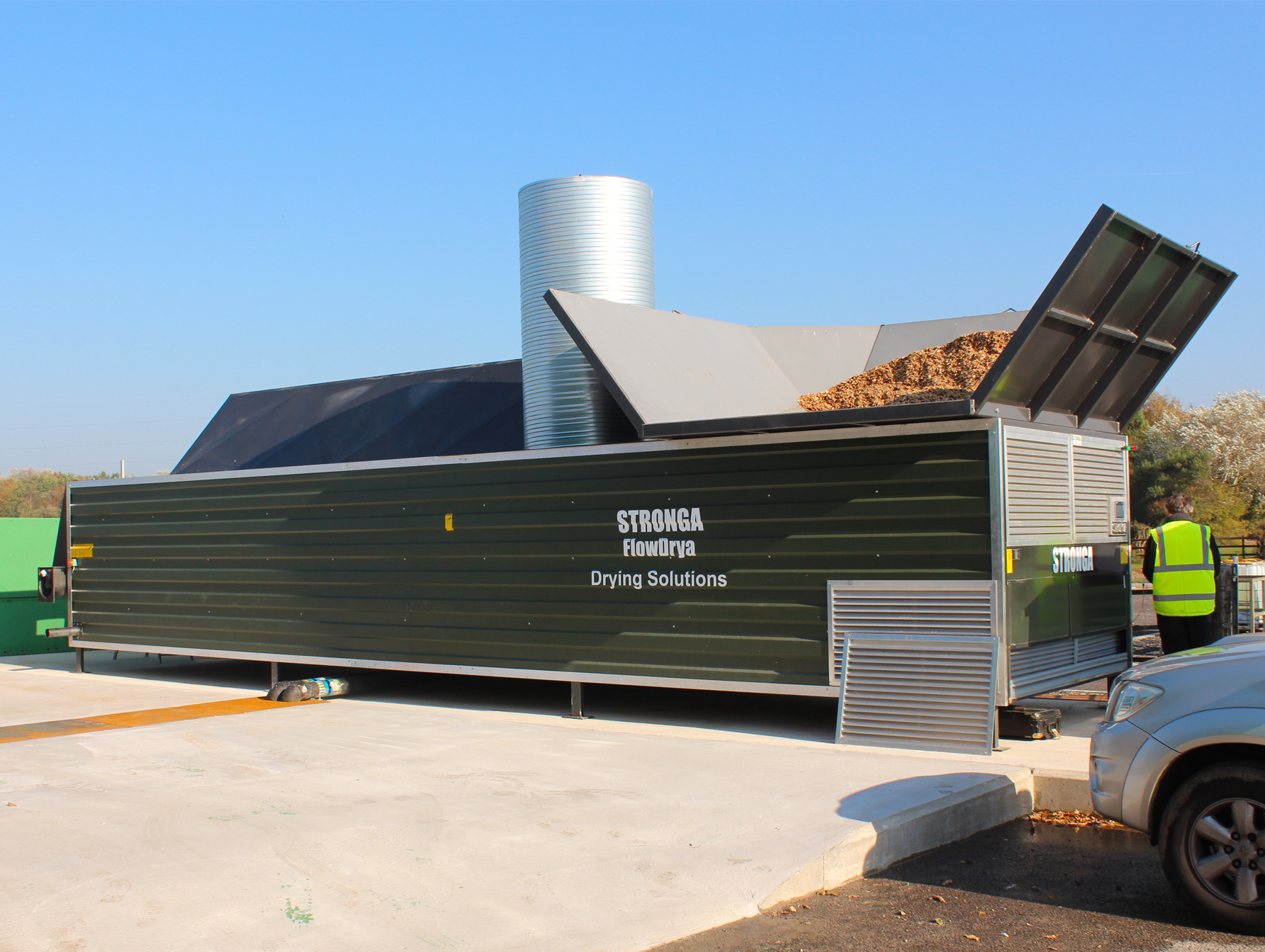
By harnessing the power of residual wood energy, our client isn’t contributing to native tree felling and is instead, by investing in FlowDrya equipment, reducing the emissions associated with burning wet wood. Drying residual woody biomass, the business are able to increase combustion efficiency, yield and calorific value, allowing them to remain competitive in an industry undergoing big growth. Both their sourcing methods and choice of sawdust drying system meet the strict Australia regulations in place for pelleting.
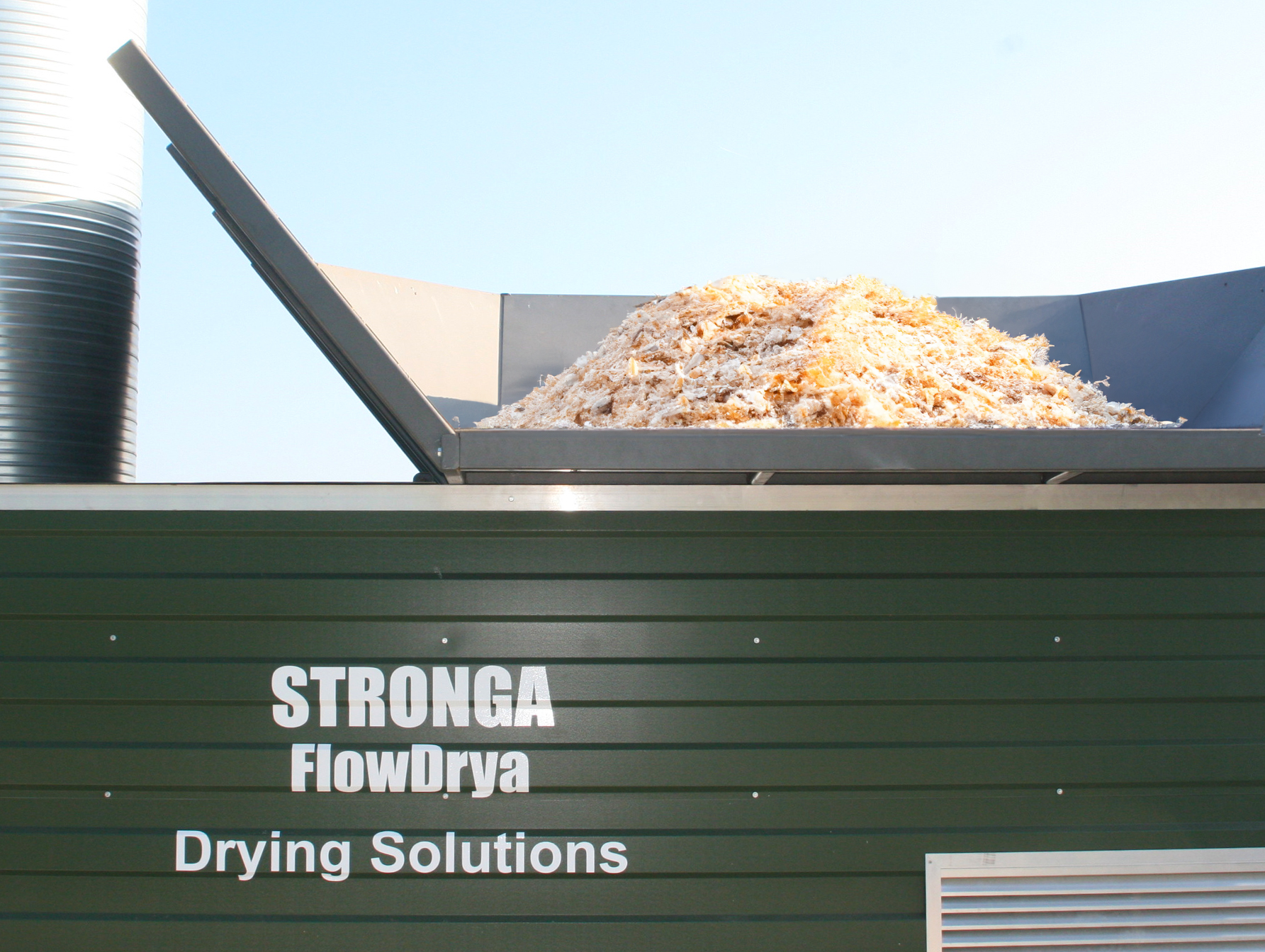
Drying at the Centre of the Pellet Production Process
Drying biomass before the “compressive” stage is an essential step in profitable pellet production. Not only does drying limit ash, VOC emissions and micro-pollutants, it also significantly increases the energy output of pellets (calorific value). Increasingly, stringent wood pellet standards are being developed; the choice of a suitable sawdust dryer is a critical decision when accounting for a large part of the overall energy demands of the process.
Drying is commonly considered the most energy-intensive part of the process, however, forced air drying has a number of variable parameters affecting output and efficiency, including aspects that are seasonally-variable. Stronga has engineered the FlowDrya series of sawdust dryers to help clients minimise energy consumption and optimise drying efficiency, providing a more effective, safer and greener dryer for more sustainable pellet production.
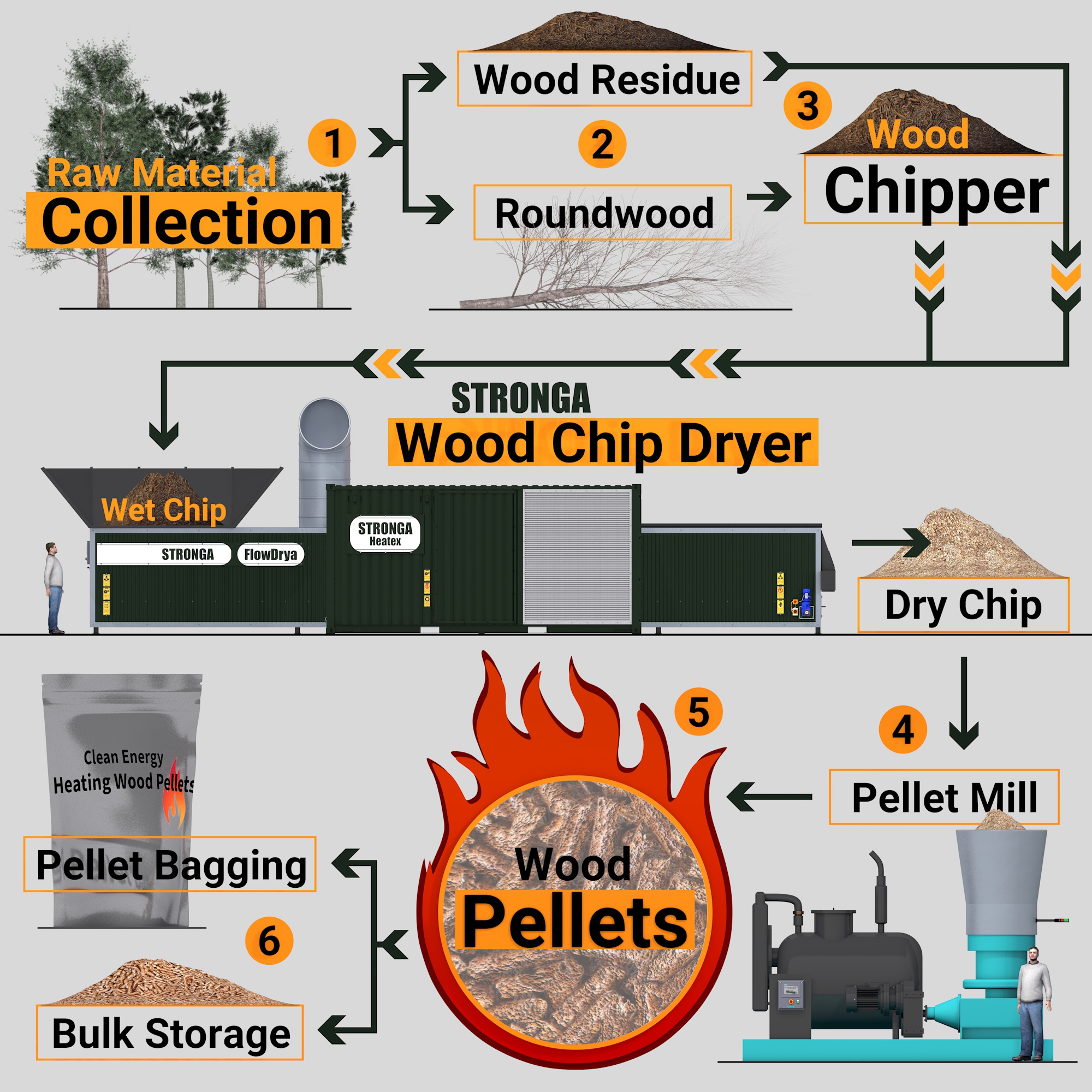
Invest in Iconic
With a local source of sustainable wet sawdust but an inefficient, existing drying process, this Tasmanian pelleting company needed to boost their pellet production from 3.5 tonnes an hour to at least 10 tonnes an hour to optimise the capacity of the pellet mill. Their existing rotary dryer was causing issues in their production process, dramatically limiting the amount of woody biomass that could be input into the pellet mill, causing it to operate at a significantly lower output.
Together with the client, Stronga developed a sawdust drying system that would make full use of residual heat from the existing rotary dryer, allowing the mill to produce pellets at full capacity. The FlowDrya sawdust dryer quickly became central to the client’s goal of maximising income, sales value and overall profits.

A Masterpiece in Moisture Removal
Acting as a ‘pre-drying’ unit, in this case, FlowDrya was synchronised to project parameters using onsite residual heat from the rotary dryer’s warm output air. This air is recuperated via a gas-to-heat exchanger to enable the site to increase value with higher output. Using the FlowDrya increases sawdust output by circa 300% without increasing energy demands.
FlowDrya’s simple and robust design is fully assembled and pre-commissioned at Stronga’s factory which ensures installation on the customer’s site is seamless. Read the other benefits of FlowDrya below:
- FlowDrya can operate efficiently using residual heat energy, allowing for energy costs to remain low, whilst wastage is minimised and efficiency optimised.
- Well-developed HMI DryStation™ controls and large in-feed hopper capacity minimise labour and handling costs.
- FlowDrya has been designed to handle even the wettest of materials and can be configured to customer-led parameters.
- FlowDrya has a unique, built-in hydraulic agitation drying bed system which is particularly effective with sawdust feedstock. Deep mixing allows for consistently dry output while issues of over/under-drying are eradicated.
- FlowDrya is super quiet and fully insulated which ensures minimal heat loss and noise pollution.
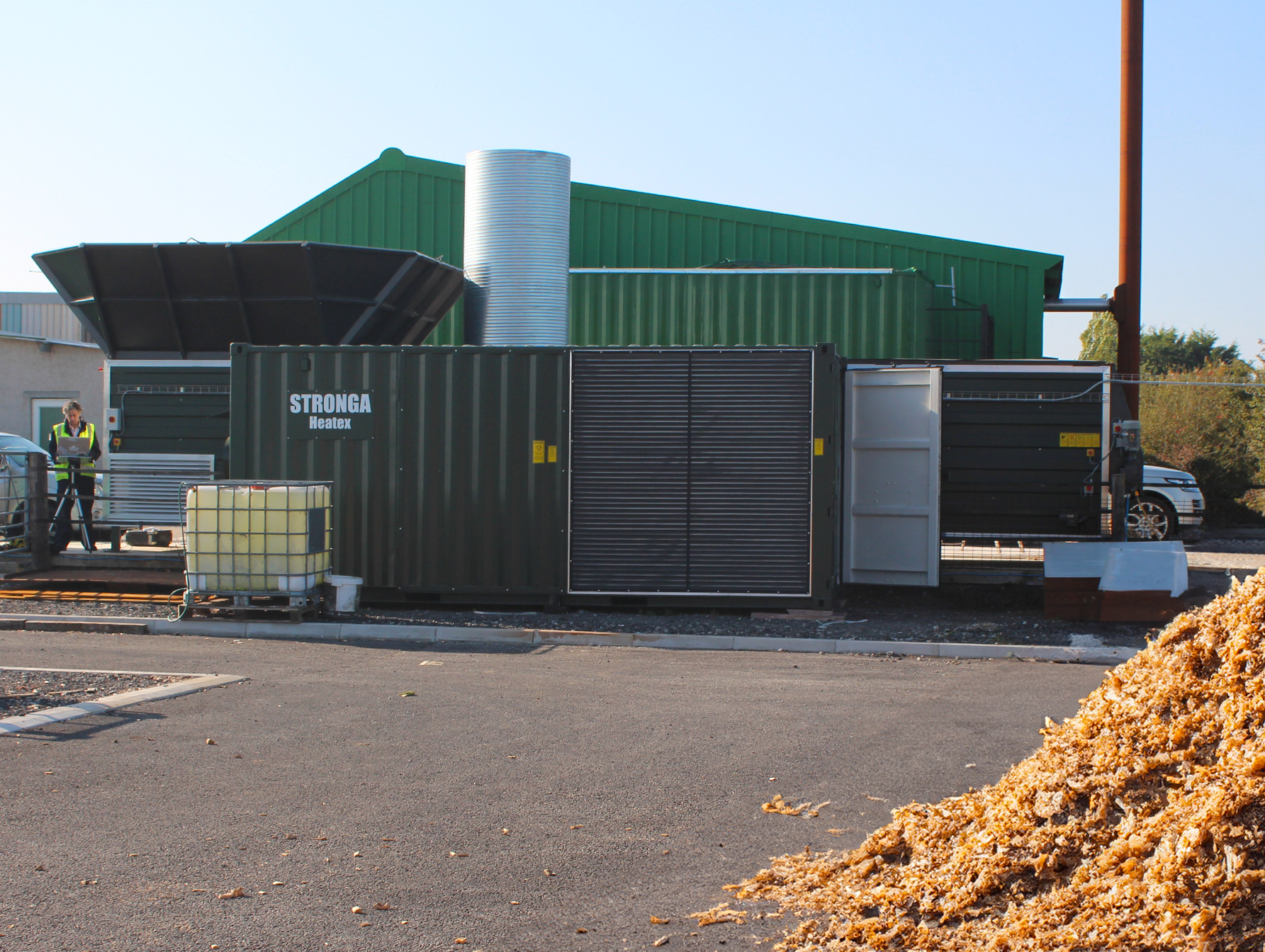
- A combination of low temperature drying together with in-direct air supply, in addition to no bearings, belts and minimal moving parts, ensures FlowDrya equipment has a super low fire risk.
- FlowDrya’s stop-start system, which cuts maintenance requirements, reduces component wear by 4X, only ‘working’ when necessary, ensuring a long and reliable service life.
In this more challenging case, where the client already had a pre-existing but in-efficient rotary dryer, Stronga scaled the FlowDrya for use in-front of the process, commissioning a heat exchanger to productively utilise the specified residual on-site exhaust air. Using FlowDrya enhances and supports the pelleting process; production was matched so pellet outputs could be produced to meet required standards.
Stronga have been developing biomass dryers for decades. Get in touch with our technical team today and begin a collaborative journey towards more sustainable and productive biomass drying, pellet production and renewable energy formation – info@stronga.co.uk
Share this post